Lighter, smarter HUMS take flight in the air medical sector
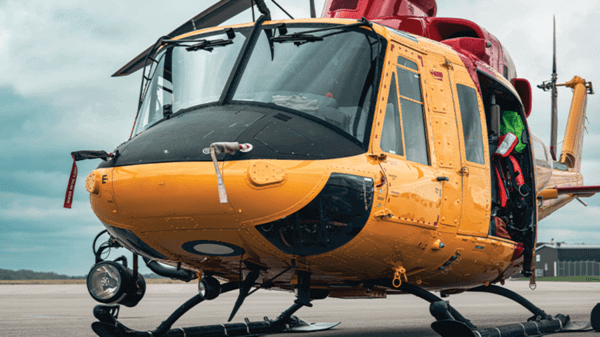
Technological developments have made health and usage monitoring systems much more viable for the air medical and rescue helicopter market. Kerry Reals explores the extent to which HUMS need to transmit data in real time
Health and usage monitoring systems (HUMS) have been slow to take off in the air medical and rescue helicopter sectors due to traditionally high installation costs and heavy weight penalties. This is beginning to change, however, with technology improvements ushering in a new generation of lighter, more affordable HUMS solutions.
Coupled with new recommendations from organizations such as the Commission on Accreditation of Medical Transport Systems (CAMTS), which has ‘strongly encouraged‘ US-based operators in this market to install HUMS, manufacturers of these systems say they are seeing an uptick in interest from players in this space for their products.
“Those first- and second-generation HUMS systems were very, very expensive and very, very heavy,” said Ronnie Ries, Vice President Of Marketing at GPMS – manufacturer of the Foresight MX HUMS system, which is in the process of being certified on multiple light and medium helicopter types. “The weights and costs when you’re operating a $20-something million aircraft that can lift 20,000-plus pounds is negligible – the safety aspect is worth it. But it was never able to bring that technology down to the medium side and especially the light side of the market because it was just too heavy and expensive,” he added.
Foresight MX is ‘significantly lighter and significantly less expensive’ than traditional HUMS systems, said Ries, and ‘that’s why operators are really starting to take a look at adopting it’. The system weighs in at 4kg (8.8lb), compared with weights of over 45kg for traditional HUMS solutions.
“The market penetration right now in this [the air medical and rescue helicopter] segment has been historically very low because it was always too heavy, so we’re now just coming to market with the certifications required for where most of these aircraft are operating,” said Ries.
Foresight MX is certified for use on the Bell 407 and 429, as well as the Airbus AS350 and H125 helicopter platforms. It is also undergoing certification on the Airbus H135 and H145. Helping to secure Transport Canada and US Federal Aviation Administration (FAA) certification on the H135 is Foresight MX customer Blackcomb Helicopters, which plans to install the system on three EC135 T2s.
Safety, operational and maintenance benefits
Blackcomb Helicopters President Jonathan Burke said he anticipated certification on this aircraft type before the end of this year. The Canada-based operator, which offers emergency services including firefighting, medical evacuations and search and rescue, is also ‘investigating’ the possibility of installing Foresight MX on its fleet of six Bell 212s.
Our primary reason for installing HUMS is that it is a requirement of one of our major customers. Secondarily, but no less important to us, we are looking forward to the predictive maintenance capabilities of having HUMS installed
Outlining the decision to select GPMS’s solution for the Blackcomb fleet, Burke said: “Our primary reason for installing HUMS is that it is a requirement of one of our major customers. Secondarily, but no less important to us, we are looking forward to the predictive maintenance capabilities of having HUMS installed.”
Ries anticipates that customers will increasingly list HUMS installation as an operational requirement, in light of a new recommendation in the CAMTS 12th Edition Accreditation Standards which ‘strongly encourages’ it.
“Between that and the US Helicopter Safety Team (USHST), they’re all saying that HUMS and FDMs [flight data monitoring systems] are two of the best technologies to help reduce accidents, especially fatal ones,” said Ries.
“I don’t think that there’s necessarily going to be a regulatory requirement, but what you’re really seeing is operational requirements or contract requirements that say ‘in order to win this contract you need to have [HUMS], because I want to know my patients are safe every time they take off’. You’re going to see more and more people requiring it in their contracts,” he predicted.

Daniil Ravvin, Senior Product Manager for Honeywell Aerospace’s HUMS and Aircraft Data Gateway (ADG) portfolio, agrees that the HUMS market in the air medical and rescue helicopter sector will grow. However, he expects growth to be ‘gradual’ because there is no legal requirement to install these systems.
“Despite defined value and the key benefits of HUMS, these systems are not mandated to be placed on aircraft,” said Ravvin. “Focus is often given to mandated equipment due to operators’ cost constraints.” He notes that Honeywell’s 1134 advanced HUMS and RECON next-generation HUMS solution are ‘very suitable for the light helicopter and air medical and rescue market’.
Despite defined value and the key benefits of HUMS, these systems are not mandated to be placed on aircraft
Addressing the benefits of HUMS on the maintenance side, Burke said that while ‘at this point we do not have good data on expected savings, we do not expect it to be insignificant’. He added: “While cost savings are important to our operations, the ability to better predict maintenance and be more proactive in maintenance planning is the primary benefit we expect to see. This will result in cost savings due to less downtime for aircraft on ground (AOG)."
Early warning notifications
Older HUMS systems provided information on the trends of various components up until the last flight hour, enabling operators to see if a part was starting to fail. Today’s systems, however, can give operators much more advance notice of when a component might start to show signs of failure in the future.
“One of the unique things that Foresight MX does is that, based off our patented algorithms, we can tell you – sometimes 100-plus hours in advance – when that component is going to become unreliable,” said Ries. “Traditional HUMS would say ‘it’s starting to go bad’. With us, we would tell you when we think it’s going to become unreliable so you can pre-plan maintenance.
“The other aspect is that, because you’re starting to see that wear and tear going on much earlier in the process, you may be capturing it when you can repair it at a bearing level instead of at a gearbox level. With HUMS, you’re creating that cost saving of doing more preventative maintenance than catastrophic failure maintenance.”
With HUMS, you’re creating that cost saving of doing more preventative maintenance than catastrophic failure maintenance
Foresight MX automatically uploads this type of data through a cellular connection post-flight, although Ries noted that GPMS is ‘exploring capabilities of doing that more in real timeʼ. One company that is marketing a more real-time product is SKYTRAC, which has developed a connectivity solution that sends HUMS early-warning notification alerts when in-flight exceedances are detected.
In addition to monitoring HUMS parameters in real time and alerting ground crews during flight, SKYTRAC’s solution wirelessly transfers HUMS data post-flight through Wi-Fi or cellular networks. This, says SKYTRAC Director of Business Development Jeff Sherwood, saves operators time and money because it negates the need for somebody to physically offload the data after every flight.
“There are hundreds of sensors and many systems on each aircraft that collect these parameters – anything from the vibration in the rotor blades to oil pressure to engine performance data. All of that information is captured by the HUMS on the aircraft,” explained Sherwood, adding that factory-installed HUMS have traditionally required ‘someone that can go out to the aircraft and download the data’.
This can result in significant costs, particularly for large-fleet operators with multiple aircraft such as Gulf Helicopters Company (GHC), which selected SKYTRAC’s connectivity solution in 2019 to support its Leonardo AW139 and AW189 HUMS and FDM programs.
“If you think about how much time that can take – per download you’re talking about at least an hour, maybe two hours of one person’s time. Multiply that by doing it once a week and then by the sheer number of aircraft they have, and you have a significant investment of resources and personnel that need to be trained,” said Sherwood. “That’s where we’ve identified some potential areas where SKYTRAC’s connectivity solutions can reduce some of that turnaround time, reduce some of the burden on our customers and also provide some more advanced functionality.”

Much higher bandwidth
Recent progress in satellite technology has made significantly more bandwidth available, enabling SKYTRAC to build a solution that can send much more data through the connectivity pipe than was previously possible. SKYTRAC exclusively uses the Iridium satellite network to power its HUMS alerting solution.
“One of the historical limitations has been the amount of bandwidth or the speed of the internet, if you will, over the satellite network,” said Sherwood. “Historically, we had been limited to sending short codes or short messages saying ‘oil pressure is unsafe’, and you would have to land the aircraft to get the full data set.”
Having an IP connection to the aircraft means that engineers on the ground can make a direct connection to find out more information about maintenance anomalies while the aircraft is in flight
In 2019, however, Iridium completed the launch of 75 new low-Earth orbit (LEO) satellites to form its NEXT constellation. “What this did was introduce much higher bandwidth services over the network, so now you have the ability to stream video over the satellite, you have the ability to access Netflix and browse the internet,” explained Sherwood. “What this ultimately allows us to do from a HUMS perspective is that if you have an exceedance notification that is triggered, or an anomaly or alert, now we can also send all the important data around that anomaly over the satellite network down to the ground, so you can have the entire data set sent.” Having an IP connection to the aircraft means that engineers on the ground can make a direct connection to find out more information about maintenance anomalies while the aircraft is in flight.
“If you have a maintenance person that wants to be able to query certain parameters and see what these parameters are looking like on the aircraft – if the vibration is staying stable or if oil pressure is consistent – this essentially allows them to connect to the aircraft and the system itself,” explained Sherwood. “So you can connect with the aircraft over the satellite network, pull all the data that you would like and, essentially, have a full internet connection.”
But not everyone is convinced about the business case for real-time, in-flight transmission of HUMS data. Ries, for instance, said that most HUMS systems monitor trends rather than ‘zero to 100 catastrophic failures’, therefore ‘we don’t necessarily see the need for real-time HUMS because most of that can be done post-flight’. GPMS is, however, exploring real-time capabilities to report flight exceedances, such as over-speed or over-torque incidents, he added.
Ravvin pointed to the cost side, noting: “There are regulations and significant operator costs associated with real-time over air data transmission. Hence, current Honeywell HUMS solutions transmit data post-flight. However, Honeywell products have the ability to monitor for critical indications, and display and send the indication or alert to a connectivity device within the aircraft for in-air transmission to the ground.”
HUMS of the future will utilize faster, secure cellular and SATCOM channels
Looking to the future, Ravvin expects HUMS to become even smarter, lighter and smaller than today’s products. “Like any other technology, the systems must keep up and be ahead of technological changes, including smarter sensors, faster data aggregation and larger data storage,” he said. “HUMS of the future will utilize faster, secure cellular and SATCOM channels. Size and weight are a key value factor for any helicopter operator, so HUMS will become modularized, smaller in size and lighter in weight.”

January 2024
Issue
In the January/February edition, we get swept along by swiftwater rescues; we land upon the qualities that make good helipads; we monitor the rise of HUMS on mid- and light-weight aircraft; and we channel the recent advances in avionics; plus more of our regular content including a heart-warming air ambulance case study for the new year
Kerry Reals
Kerry Reals is a freelance journalist with two decades of experience covering the global airline industry, with an emphasis on the sector's sustainability efforts. She is a regular contributor to a range of trade publications, including Flight International, Airline Business and Via Satellite. Kerry previously worked at FlightGlobal where she held a number of senior editorial positions, most recently Group Deputy News Editor. She has also had work published in the national press on subjects ranging from sustainable transport to parenting.