Interview: Nicole Kunter-Hudson, CEO, Air Ambulance Technology
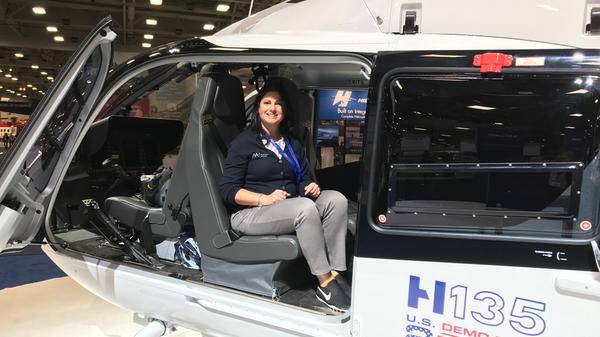
AirMed&Rescue caught up with Nicole Kunter, CEO of Air Ambulance Technology, to discuss recent innovations and celebrate the company’s 25-year anniversary
What projects have you been working on recently?
Air Ambulance Technology works closely with OEMs such as Airbus Helicopters and Leonardo, and also designs and manufactures medical and VIP interiors for private operators, governments and militaries. One of our recent projects was with Rotor Korea, designing an EMS interior for a Leonardo AW189 that can be adapted to fit the specific mission. Another recent project was a completely new system, developed not so long ago for a Brazilian customer who needed an EMS interior for an H135. This interior can be installed and removed within five minutes and can offer full intensive care treatment if necessary. A Finnish customer needed an interior for an AS332 which, apart from the stretcher, wasn’t attached to the floor. The reason behind this was to protect the equipment against salty water being brought into the cabin during a rescue mission at sea.
Air Ambulance Technology has been designing medical aircraft interiors for over 25 years, and since the founding of the company, all of these interiors have given the operator the possibility of flying multi-missions on the same day.
Could you explain the process of customisation of a helicopter interior?
Firstly, the customer explains which mission profile has to be flown, and in which aircraft. For example, SAR, inter-hospital transport, mountain rescue etc., to be flown in an H135, AW139, Bell 412 etc. We then design an interior that fits the profile. Important aspects of the design process are: which medical devices are to be used? Do the batteries of the medical devices need to be charged whilst the aircraft is in flight? How long is the maximum flight time? This is important to know how much oxygen will be needed. Testing has been or is carried out on all our interiors up to a force of 20G. We generally have a lead time of approximately three to four months from start to finish for an existing Supplemental Type Certificate (STC), but for new STCs, a lead time of up to nine months must be taken into consideration for certification. Our quickest start to finish time was for an American operator who visited our company in February 2018, and had his interiors installed in two EC135s in April 2018, a little over two months later.

When it comes to obtaining an STC in European and the US, what are the main differences between EASA and the FAA’s requirements?
Being an Austrian company, all our interiors firstly receive an EASA STC. These EASA STCs can then be transformed to FAA STCs, normally quite easily. On top of this, our interiors are validated for the specific country where it is to be flown. For example, in China we validate our interiors with the CAAC, or in Japan we get a JCAB validation.
When did AAT develop its ‘quick change technology’ and how is this different to other modifications on the market?
My Father, Egon Kuntner, developed Air Ambulance Technology’s ‘Quick Change Technology’ 25 years ago. As far as I know, we were the first company worldwide to offer this to our customers. Our Quick Change Technology has many advantages for the customer; it’s not only easy to remove and clean and disinfect, and re-install within minutes, but the interiors can be installed in helicopters used for other missions, such as police, Air Force, fire brigades, etc. at times of natural disasters, or medical evacuation missions. Also, when a helicopter is replaced by an operator, the interior can be removed and installed in the replacement helicopter if it is of the same type. As far as I am concerned, there are no disadvantages with our products. Also, a dedicated EMS helicopter/aircraft is probably a lot harder to sell than trying to sell a helicopter/aircraft with a re-installed PAX configuration.
How has the development of new tech such as 3D printing changed the way in which AAT works?
To date, Air Ambulance Technology hasn’t needed to use 3D printed parts. All our interiors and the parts they are made of are manufactured in house. We have our own machine park with CNC 5 axis lathes, laser printers etc., and are therefore not dependent on other companies.

How do you see technology moving on in the future, and how can this be applied to helicopter interior modifications?
This is, and will always be, a difficult question to answer. There are many new technologies on the market waiting to be explored. Whether it be wireless communication, this meaning that the hospital knows what injuries the patient has before he even gets there, or anti-bacterial coatings, lighter more durable fluid and fire-resistant seat coverings. We are very busy in our innovation department developing and testing new ideas that maybe one day can be found and used in our interiors. Air Ambulance Technology doesn’t just think about new technologies and products, but also about using recyclable materials. The main material used for our interiors is aluminium, it can be melted down and re-used when necessary. As a company we also like to do our part for the climate.
Powered loading technology seems to be very popular with those who operate helicopters that can take the additional weight; is this something that you are developing?
This is a great question, and to answer it truthfully, yes, maybe! Powered loading technologies go against nearly every helicopter operators’ principles. The interiors should be lighter, cheaper, and maintenance free, which our interiors are. On the other hand, powered loading technologies are unnecessary weight, have batteries which are also unnecessary weight, and are definitely not maintenance free. Powered loaders are great for inter-hospital patient transfers, but for rescue missions they are unpracticable. Also, powered loading is only useable in countries where a stretcher has an undercarriage and can be rolled on hard ground. I would love to see Bhutan Air Rescue using a powered loader whilst balancing on the side of a mountain on one skid. Or an Alpine air rescue mission push the wheels of a stretcher through the one-meter-deep snow up to the back of a helicopter and start using a loading aid. Powered loading is great for tarmac, concrete etc., but as soon as you have soft or uneven mountainous ground, the patient has to be carried and lifted into the helicopter on a lightweight stretcher, and not a stretcher with an undercarriage weighing in excess of 50kg. On the other hand, we produce bespoke aircraft interiors, what the customer wants, the customer gets.

What are you doing to mark the occasion of over a quarter of a century in this business?
The company was founded in November 1993, so this November we will be 26 years old. The reason we have waited until now to celebrate is that my parents, Dorothea and Egon Kuntner, the founders of the company, will be laying down the tools of the trade, and going into retirement. Over 25 years ago, they had five employees and rented an office and a few square meters of a workshop in the company next door to the present Air Ambulance Technology headquarters in Ranshofen, Austria. Today the company has a 3280-m2 building employing in excess of 45 highly skilled and qualified people. Building a company from the ground up over the past 25 years that doesn’t manufacture just a product, but manufactures one that helps save people’s lives, has to be celebrated.
What do you enjoy most about your job?
I started working for my parents over 25 years ago. I have seen the company grow from one office and five employees, to a company with 45 employees and its own machine park and assembly hall. Since 2014, I have been working full-time in the company, and have been CEO since 2016. I have witnessed many products leave our company. With every new idea we go on an exciting voyage of discovery. Every customer’s requirement is unique, as is every implementation solution that leaves our house. We develop each and every concept specially for the needs of the customer and are always searching for even better solutions. With these solutions we like to surprise our customers, and sometimes, even ourselves. Who could wish for a better job than this?!
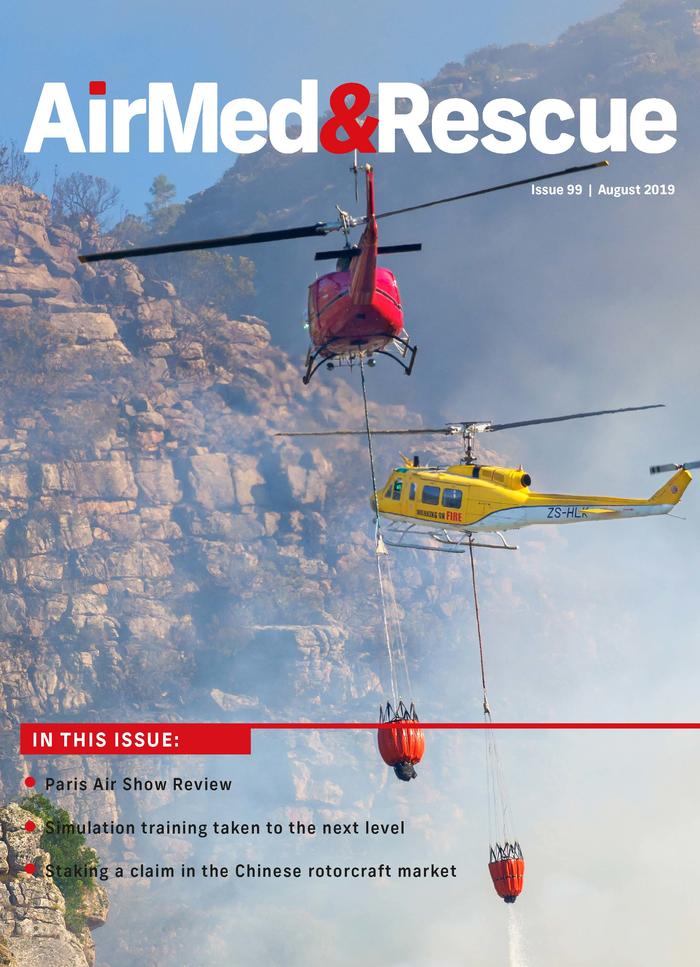
August 2019
Issue
In the issue:
Paris Air Show Review
Simulation training taken to the next level
Staking a claim in the Chinese rotorcraft market
Industry Voice: A crash course in risk management for SAR crew
Breaking the mould: A new anti-spin device for hoist rescues is being tested
Interview: Nicole Kunter, Managing Director, Air Ambulance Technology
Subscribe to be notified by email when the latest issue is published each month.
Mandy Langfield
Mandy Langfield is Director of Publishing for Voyageur Publishing & Events. She was Editor of AirMed&Rescue from December 2017 until April 2021. Her favourite helicopter is the Chinook, having grown up near an RAF training ground!