Air ambulance interior design and technology
The interior of an air ambulance has to be meticulously designed to incorporate the right equipment, and ensure that this equipment is to hand when the medical crew needs it. Mandy Langfield considers the latest developments in aircraft interior design
It all starts, of course, with the selection of the aircraft itself – its size, its adaptability and its original purpose. While there are still jets in use that were originally designed as business aircraft and have been adapted for medical use, the more modern aircraft available for purchase are designed to be multi-purpose from their inception, and are thus better suited to their roles when it comes to ergonomics, ease of access to, and loading of, patients, and enhanced comfort for crews.
Pilatus had already enjoyed success with air ambulance operators thanks to its PC-12, which was rugged enough to cope with unpaved runways in Australia and Africa and pick up patients from the most remote locations in these areas. Its new PC-24 has improved on this template, with an increased operations level and faster top speed making it even more in demand. The fact its cabin altitude can be maintained at sea level up to Flight Level 230 is a specific bonus for critical care. Ignaz Gretener, VP General Aviation at Pilatus, told AirMed&Rescue: “Based on the demanding customer requirements, Pilatus offers a fully customised medical interior which was developed in a joint partnership with a renowned Swiss EMS interior manufacturer after the latest standards in industry.” Aerolite is the aircraft’s interior manufacturer, and the development of the design for the air ambulance interior also had input from the Royal Flying Doctor Service, which hopes to accept its new aircraft in October and November of this year. Oscar Schwenk, Chairman of Pilatus, said that the air ambulance market is ‘a perfect fit’ for the PC-24: “This is a growing niche,” he says, “and the PC-24, with its many features – such as a large cargo door, roomy cabin and short-field performance – is a perfect fit for this market.”

Roland Hengartner, CEO of Aerolite AG, noted that the Pilatus PC-24’s wider cargo door means that in developing the customised medical interior, Aerolite could take advantage of the increased size with a stretcher loading device that allows for easier and safer patient loading.
Martin Siegrist, Senior Vice-President Technical at LCI, an aircraft leasing organisation, pointed out that patient care is now a key driver of aircraft design, particularly helicopters. He said: “The dimensions of the cabin, and the space available for medical crew to operate in, must be optimised to permit full access to the entire patient body from both sides at all stages of the flight. High ceilings provide for a more comfortable working environment, as does the ability to rotate and move the platform.”
The capacity to choose between different cabin configurations (i.e. positioning the stretcher in transversal or longitudinal direction) means that aircraft can also be further optimised for different mission types. “A wide and regular cabin allows medical equipment to be stored in dedicated areas close to the patient and easily accessible to the medical crew,” said Siegrist, “while the provision of a spacious, separate bagging compartment means that rescue equipment can be stored without compromising the working environment.”
Gulfstream has made considerable advancements in medevac cabin design over the years – from the functionality of the medical environment to medical crew ergonomics
Gulfstream Aerospace Corporation offers a wide variety of interior customisation options, as it configures each medevac aircraft based on each customer’s specific needs. “Every medevac aircraft is equipped with an electric patient loading system and can include a wide array of options,” explained Rich Nevitt, Director for Gulfstream’s Special Missions business development unit. “Typical integrated systems include oxygen, suction and compressed air components, permanent medical beds, ample oxygen capacity and electrical outlets for medical equipment. All Gulfstream aircraft are engineered for passenger and patient comfort, with 100-per-cent fresh air distribution, soundproofing and low vibration.”
Gulfstream has made considerable advancements in medevac cabin design over the years – from the functionality of the medical environment to medical crew ergonomics. The company recently designed and delivered a state-of-the-art Gulfstream G550 medevac to the Beijing Red Cross Emergency Medical Center. With the admirable aim of revolutionising in-flight medical care, the aircraft has been designed to provide emergency crews with the most effective – and safe – access to patients possible. “For example,” continued Nevitt, “the aircraft features a transitional operating table for 360-degree in-flight patient access – a medevac first. An exclusive patient loading system and well-positioned medical equipment provide safe and efficient access to and from the aircraft’s cabin.” Gulfstream medevac interiors are designed with many of the same health attributes as other Gulfstream aircraft – including low cabin altitude pressure, advances in noise reduction and 100-per-cent fresh air. These optimal features contribute to an ideal medevac environment for critical care patients – and for medical professionals providing life-sustaining support.

What’s on the inside
The design of an aircraft cabin interior is key to its success as an air ambulance. Starting from the bottom up, the need for sealed heavy-duty flooring and washable interior liners is essential, and new materials coming on the market make these needs easier to fulfil. Aerolite has worked on B200, Challenger CL604 and Learjet fixed-wing aircraft, as well as a number of medical helicopters. It has developed a multitude of options over the years, demonstrating the wealth of choice now available to air medical operators. As companies often operate a variety of aircraft for air medical transfers, it is vital to have customisable options available.
Aerolite’s integral floors are either one or two-piece machined aluminium assemblies, which provide points for mounting internal equipment in seat rails and at attachment points at the front. The EMS integral floor has a raised lip around the edge to contain any spillage and two drain holes at the front LH and RH sides, which mate with floor drains during installation. Running boards at the cabin doors give protection to the edge of the floor and provide non-slip surfaces. Attachment to the floor of the rotorcraft is made using track fittings, stops and screws.
Spectrum Aeromed, based in the US, provides customised medical interior solutions to air ambulance companies around the world. Thomas Redder, Vice-President of International Marketing, told AirMed&Rescue that the team is ‘constantly listening’ to feedback from medical crews and air ambulance operators in order to enhance their offering, including organising Kaizen events to work on product improvements together. Some of the latest trends in customer demand that the company is seeing include:
- New electrical interfaces (e.g. USB connectors).
- Ease of disinfection.
- Integration of more complex medical devices (e.g. ECMO units, isolation chambers).
- Longer distances for flight (fewer fuel stops but require more oxygen).
- Proper mounting of medical devices.
- Modular concepts to allow flexible system configurations.
Siegrist of LCI said that there is a range of new material and technology available including new, lightweight equipment, easier to clean surfaces and amenities that enable greater comfort for patients. He added: “A key factor is certification standards for brand new helicopters which are becoming ever stricter in order to maximise safety, and this in turn impacting weight constraints faced when operating helicopters. As a result, we are likely to see the development of extremely compact medical devices for use in EMS operations.”
LifePort, a US-based company that designs and fits medical interiors into aircraft of all shapes and sizes, said that custom cabinets, additional storage underneath stretchers, and new-generation seats are examples of ways in which the company is optimising design to increase efficiency and comfort for both patients and crews. When it comes to the easy-clean surface options, the company uses LifeGard, which provides anti-bacterial/anti-microbial surfaces, while the use of custom-designed floor overlays protect the aircraft from foreign fluid contamination. “Thicker mattresses, wider stretchers, and powered loading systems are all utilised to increase patient care and comfort,” explained Michelle Wynne, Head of Marketing and Communications for LifePort.
When it comes to the materials being used, Wynne explained that the use of new lightweight materials is dictated by a customer’s budget, and are specific to their operations, so there is no ‘one-size-fits-all solution’. She added: “Utilisation of carbon fibre, traditionally-machined aluminium, and 3D printed parts are all applications that we look to exploit.”

For clients, the process of selecting a medical interior remains the same. Once they have determined their requirements, based on their mission profile, a budget evaluation can then take place. Wynne explained: “The budget drives the use of lower-weight materials over their lower cost, depending on customer priorities.” To limit additional expenses, existing designs are used where possible, although this can again be affected by budgetary constraints.
Medical advancements also mean new challenges for medical interior companies. Ricky Reno, Vice-President and Account Executive at Spectrum Aeromed, said that as new medical devices are used, new mounts need to be designed to accommodate these inside the aircraft. He explained: “With the development of the medical mounts, Spectrum Aeromed has designed new ways of mounting the medical mounts. Spectrum has designs for dedicated aircraft interiors using rail systems to attach the mounts. For multi-mission aircraft, Spectrum has designed a medical wall that attaches to the life support system, free from the interior walls to attach medical devices to. The medical walls are manufactured out of aluminium or new lightweight composite material.” If the air ambulance operator does not want a medical wall, but still wants to be able to secure medical devices, Spectrum has designed a stretcher bridge that attaches to the stretcher. The stretcher bridge allows the medical team to secure the medical devices to the stretcher while transporting the patient from the aircraft to the ground transportation without removing the medical device from the patient, or laying the device on the patient during the transition.

Metro Aviation has developed customised medical interiors for medical helicopters across the US
Metro Aviation, which operates one of the largest fleet of air medical aircraft in the US, as well as offering a completions service, has developed customised medical interiors for medical helicopters across the US. It also holds more than 30 Supplemental Type Certificates (STC) and completes about 35 aircraft each year for US customers and global clients. Amy McMullen, Aircraft Configuration Co-ordinator for Metro, said that the company works closely with its customers to create Federal Aviation Administration-approved mounting provisions that function for the medical crew. She added: “The STC-approved interior that was designed when we completed the Michigan EC 155’s has proven to be a sufficient interior for our EC155 customers. The additions that have been made have been new monitor mounts or stretcher solutions as new equipment arrives onto the market.”
Challenges ahead
More is being asked of pre-hospital emergency care providers, and international air ambulance operators, when it comes to the critical patients that they are transporting. With more complex patients come more complex medical devices, and thus, space and weight restrictions mean that lighter and smaller is the way for the future. With that in mind, carbon fibre and 3D printing may well unlock how air ambulances of the future can provide the right care with no compromise.
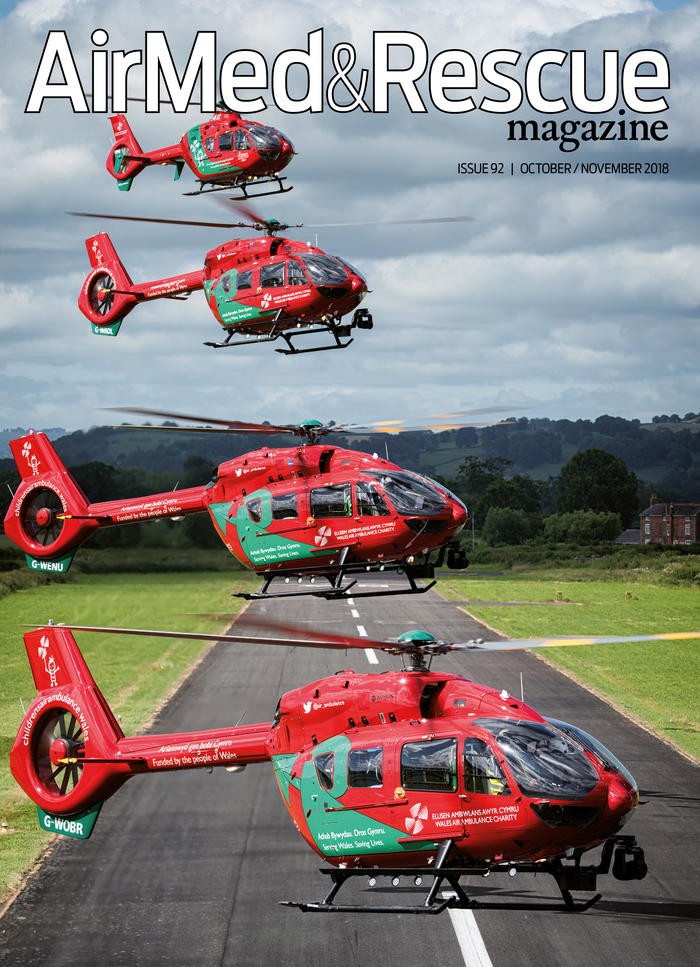
October 2018
Issue
In this issue:
Swiftwater rescues part II - Europeans do it differently
Always moving forward - Next-gen aircraft medical interiors
Mixed reality – the future of emergency medic training - Virtual training combined with reality – the best of both worlds
Generation X - The future of USAF combat rescue helicopters
Data incoming - Developments in the fast-paced world of aviation communications and technology
Interviews:
Dave Kelly - Co-Pilot, Essex & Herts Air Ambulance
Mark Delaney - General Manager, Toll Helicopters
Medical Insight: High oxygen, low altitude -Hypoxic respiratory failure and the effects of cabin pressurisation on patients with respiratory conditions
DroneSAR - Are UAVs the future of SAR?
Provider Profiles:
AeroMD -International air ambulance service based in the US Virgin Islands
California Highway Patrol Air Division - SAR, air ambulance and law enforcement, all in one
Mandy Langfield
Mandy Langfield is Director of Publishing for Voyageur Publishing & Events. She was Editor of AirMed&Rescue from December 2017 until April 2021. Her favourite helicopter is the Chinook, having grown up near an RAF training ground!