Industry Voice: Electronic flight bags
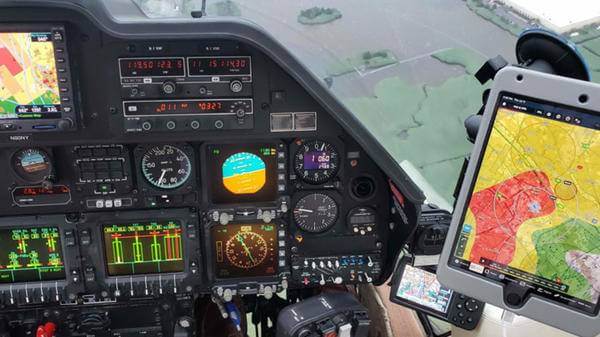
Andrew Boniface gives his take on how pilots can safely and effectively introduce electronic flight bags to their cockpits to enhance operational safety without becoming over reliant on automation
Since the release of the first iPad in April 2010, the use of these devices in our industry has multiplied exponentially. An ever-growing list of aviation-specific applications continue to hit the market for use on both iOS and Android devices, spearheaded by those with approved data service provider status. These apps undoubtedly enhance commercial efficiency, and when used correctly, also improve levels of safety and compliance.
Safety enhancement must be the focus
We all want a safer operation and safer habits as pilots, generally in the form of good airmanship. It’s important to note that use of an electronic flight bag (EFB) should not come at the expense of our non-technical skills like situational awareness, prioritising and managing tasks, and effective communication. When used correctly without over-dependence on automation, an EFB can improve our situational awareness quite successfully in the following ways:
- Reduce crew workload through faster access to information and automation of some SOPs
- Provide 100-per-cent coverage of weather, NOTAM (notices to airmen) and aeronautical information for any possible diversion
- Improve cockpit ergonomics and reduce chance of human error
- Provide ADS-B In capability for traffic to be displayed in-app (GDL90 Protocol)
- Import KML (keyhole markup language) search-pattern data, benefiting EMS and SAR responses
- Show air-law updates in real time
- Reduce corporate risk.
Introduce the technology
Setting up a commercial EFB program isn’t meant to be a daunting process, although it can sometimes seem that way. Regulators just want to see that the required checks and balances are in place for the control and manageability of your EFB programme. Where safety is concerned, compliance is never far away. So why do EFB solutions need tailoring to each organisation, and how can this be accomplished to ensure compliance?
Below are details of what the major planning considerations for your EFB programme should be.
Assign a ‘champion’ of EFBs
Giving a member of staff responsibility and ownership heightens engagement.
Engage an EFB implementation partner if required to roll out the programme
Help is always on hand should you need it.
Determine the number and allocation of devices
There are several options here:
- Device per aircrew: this provides the ultimate system for moderate- to large-sized organisations, particularly in multicrew environments.
- Device per aircraft: this requires fewer devices and is therefore cheaper, with the added benefit of a single aircraft profile per device. Please consider redundancy options, and note that this plan will not give you compliance in a multicrew environment.
- Bring your own device: this is the riskiest in terms of compliance, but is the cheapest for operators as aircrew fund and supply their own device. Regulators are not fans of these setups unless additional controls are put in place, which can also be costly.

Electromagnetic interference test
EFBs are Portable Electronic Devices (PEDs), and checks are thus required for radiation and electromagnetic interference (EMI). Many technical sources suggest the iPad has been tested and found to be compliant with the standards described in RTCA/DO-160 (Environmental Conditions and Test Procedures for Airborne Equipment) with respect to EMI testing. In many operations, the device is therefore considered suitable for general use as an EFB (in accordance with the conditions described in an EFB operations manual supplement). Despite this, PEDs should generally comply with Federal Aviation Administration order AC91.21 in the following way:
- Aircraft is designed and certified with PED tolerance, or
- Operator must conduct a safety risk assessment to evaluate the avionics configuration of the fleet (outlines mitigators and controls operational needs). The method here is generally referred to as source / victim testing, or
- If PED tolerance is not demonstrated, PED operation may be allowed during cruise flight only.
Assessment of operating conditions
These need to be accounted for and included in relevant operations documentation. Are you satisfied that the EFB is suitable, with the required mitigators in place, when limits of EFB performance are reached? Temperatures above 35°C are a prime example of when mitigators such as cooling, redundancy, hardware, or cockpit location play a part in guaranteeing EFB performance. The full list of operational conditions we must consider include:
- Temperature
- Humidity
- Ambient lighting (NVFR / IFR / VFR)
- Turbulence
- Altitude
Review the regulatory material
A thorough review is required to ensure the operations manual includes an EFB supplement (or equivalent) outlining the company’s EFB solution. This can be outsourced or completed internally when resources are required.

Determine class
When it comes to the practical side of attaching your EFB to your cockpit, what are the pros and cons of the options available to operators? When using a suction-cup or other portable solution, many regulators require the EFB device to be stowed during critical phases of flight such as during take-off / landing, below 1,000ft AGL, and when experiencing turbulence – not very practical. I was once flying a B206L in the cruise at A015 and the entire EFB assembly fell off on my cyclic arm. This event was my fault for not pre-flighting the suction cup mounting system that morning. Suction cup mounts are very reliable if checked and used correctly, but this event could also be a safety case for a permanent mount.
Permanent mounts and aircraft installed solutions require airworthiness approval, which will mean either an Engineering Order (EO) or Supplemental Type Certificate (STC). So, what’s the difference? An EO looks at the aircraft (singular or plural linking to serial number or registration) nominated in the control documentation. It is usually more of a one-off (broadly speaking), with maintenance personnel asking themselves, ‘am I affecting the airworthiness of the aircraft, or does this modification have the possibility to do so’? A design engineer will ask ‘in an accident, what could happen? What material is it made from? Plastic vs aluminium etc’?
Generally, an EO is the solution for many iPad mounting requirements. The approving design signatory is certifying that the modification is ok for a specific aircraft only. This certification also addresses any other modifications that may already have been incorporated. During the fitment process, maintenance engineers will install the part in accordance with the EO, then the design engineer uses information provided by maintenance engineers to authorise the EO. In aviation terms, the ballpark costs for a single aircraft won’t break the bank, however, for a larger fleet, it can be costly, especially when testing is required.
STCs originally grow from EOs once a business case has been presented, and the supplying company is happy to spend a (usually large) amount of money to get the STC approved. This will generally be a solution presented to industry, and larger companies usually buy STCs for this purpose. A maintenance facility can buy the component off the shelf to be fitted straight to the aircraft in accordance with the STC (installation instructions, continued airworthiness etc).
LTRMs are available for a growing list of fixed-wing regular public transport aircraft but aren’t available for the rotary-wing side of the industry … yet
The manufacturer of the component has already been through the process with the aircraft manufacturer to get the approval. STC solutions for EFBs have moderately high initial costs for installation. An STC does not always allow for future technology (and size) refresh cycles of the EFB devices. Companies like PIVOT are working with STC partners such as AKKA, navAero, ASG and Fokker Services, to provide a universal mounting point option that is compatible with any device (past, present or future). Modification by STC is generally more accepted internationally, with an existing bi-lateral agreement between Australian and US aviation authorities, for example. Engineering orders do not have the same benefit.
A third option now emerging is a Long Term Removeable Mount (LTRM), again provided by PIVOT. Technically, this is a portable setup (no requirement for EO / STC), with all the benefits of a permanent setup. LTRMs are available for a growing list of fixed-wing regular public transport aircraft but aren’t available for the rotary-wing side of the industry … yet. LTRMs leverage the existing STC / EO attachment concept and available cockpit structures / material characteristics to manually attach to the aircraft window without tools or hardware. Each PIVOT LTRM also fully adheres to the spirit and intent of the applicable guidance from FAA, EASA, and other regulators. This device can be deployed and installed in seconds, and lasts indefinitely. LTRMs have been used to replace suction cups, as an end state for EFB mounting, or as a transitional product from viewable stowage to installed mounts from a variety of licensed STC manufacturers.

Cockpit arrangement is key
With any of the above solutions, please remember ergonomics are very important when determining how to arrange your cockpit. Carefully consider the types of flying you will need to do, such as powerline survey, media, EMS etc., and how these will affect your EFB cockpit setup. Most importantly, minimal obstruction to external vision or instrumentation should occur, and control inputs should be unobstructed. It’s also a good idea to neatly house and stow charging cables when not in use. A correct EFB mounting setup can also be a countermeasure to prevent a device over-temp situation.
Determine functionality
What would you like your EFB to be capable of? Choose an approved EFB application and supplemental applications. Consider software integration requirements to streamline internal processes and determine the requirement for a certified EFB weight and balance solution.
Select hardware / redundancy
In many countries with adequate data coverage, a WiFi+ cellular device is ideal to receive pertinent information in-flight, and also for GPS functionality (this GPS limitation is specific to Apple devices, whereas most WiFi-only Android devices have GPS functionality). In areas where data coverage is not so reliable, a WiFi-only device will be adequate. In the US, for example, most aircraft are fitted with ADS-B receivers, which pick up aeronautical information (weather) at 978MHz instead of the standard 1090MHz frequency. Electronic conspicuity devices with both ADS-B In and Out can also be a good option in countries and flight categories where ADS-B transponders are not yet mandatory.
Of course, training is necessary and a legal requirement for pretty much everything we do in aviation
Subscription management
In organisations needing greater levels of control, some EFB applications can be managed by a web-based dashboard that enables compliance with the following key benefits:
- App subscription management
- Custom document library
- ALA / AD / HLS register management for those company-specific waypoints
- Lockable aircraft profiles opening the door to an EFB weight and balance approval in many countries
Mobile device management
For an even greater layer of compliance, elect for centralized iOS control and management over a fleet of EFB devices through a single portal. Mobile data management solutions can be used to remove or lock iOS features, and provide a fixed layout for control and IP protection. This is great for the restriction of iOS settings and compliance monitoring, especially for operators that have chosen the ‘bring your own device’ option for their EFB programs, where it is generally a regulatory requirement.
Training
Of course, training is necessary and a legal requirement for pretty much everything we do in aviation, and more recently, this training has become competency based. Training should include all details on hardware, software, failures / malfunctions, redundancy, and be specific to the class and functionality chosen. Aircrew must be aware of the procedures in place to ensure the latest aeronautical information has been downloaded before flight.
Human factors should be threaded through to include ways in which EFBs can enhance our non-technical skills, and also to cover the main causes of error such as fixation, distraction, lack of awareness, complacency, and over-dependence on automation when using an EFB. Currently in many countries, flight training syllabus and manuals of standards do not include EFB competencies, and new pilots are often using an EFB in flight for the first time on their own without any guidance. Yes, it is the responsibility of the pilot in command to know how to use the equipment at their disposal, but there are a few moving parts to get your head around when using an EFB for planning, briefing, and, of course, in-flight. Training content is therefore a good safety mitigator and countermeasure. It is important to provide initial training to all flight crew and EFB managers. Frequent changes in regulations, technology, iOS, and app functionality mean that annual training is a good idea to get the most out of the company EFB program. At the end of the day, we want to move threats from the latent or unexpected category to the expected category. Training assists in doing just that.
This preparation, in addition to a streamlined and well-informed deployment and adequate training, will set you up for success. At the end of the day, regulators just want to see that the required checks and balances are in place for the control and manageability of your EFB program.
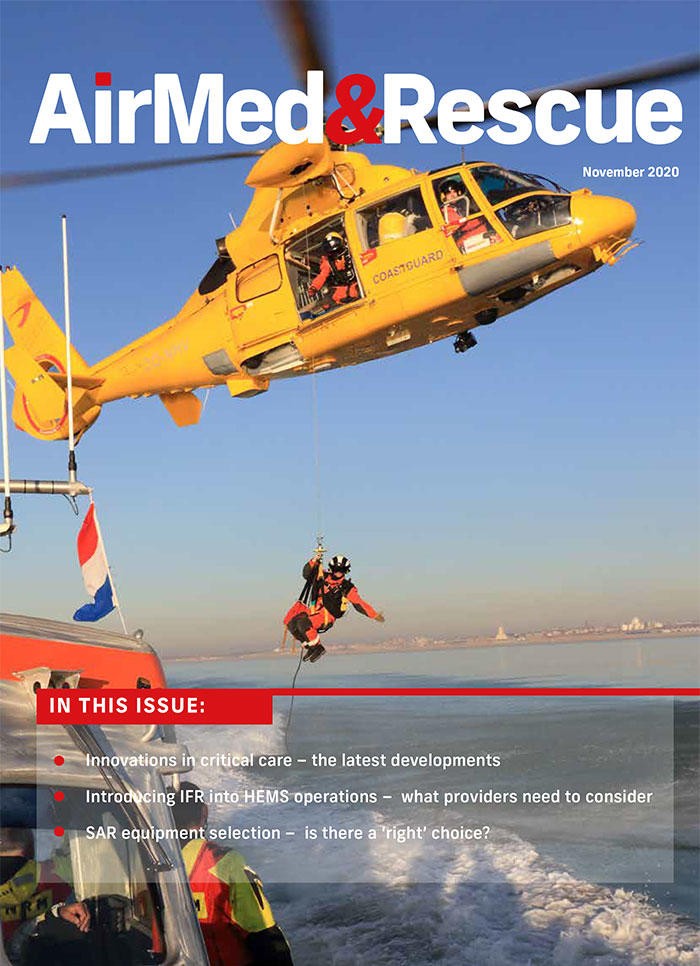
November 2020
Issue
Innovations in critical care: The latest equipment and treatment options
Introducing IFR into HEMS operations: Planning and training are key
SAR equipment selection: Is there such a thing as the ‘right’ kit?
Electronic flight bags: Practicalities of use
Interview: Kolby Kolbet, LifeLink III VP Clinical Operations
Covid-19 in LATAM: Two providers share their experiences
Provider Profile: RACQ CQ Rescue
Andrew Boniface
Andrew is a Grade 1 Rotary-Wing IFR and NVIS flight instructor based on the Sunshine Coast, Australia. Andrew also has experience flying powerline survey, firefighting, media, and general commercial operations. More recently, he has been working as Director of Aviation Consultancy, Airspace Flight Solutions, which specializes in implementing commercial EFB programmes, supplying hardware, and providing aircrew training. Clients include the Australian Defence Force, where Andrew has facilitated many training sessions around Australia on behalf of OzRunways, where he also consults.