The challenges of certifying products for aviation
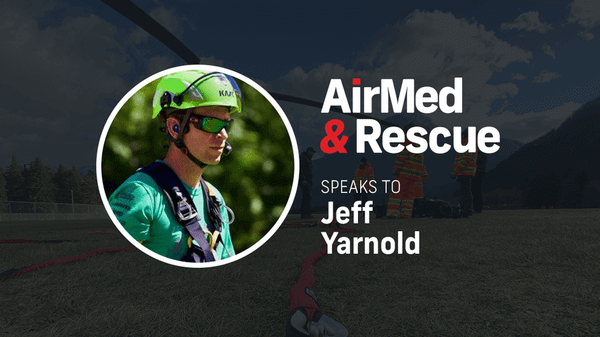
Jeff Yarnold, VP Operations at Boost Human External Cargo Systems Inc., spoke to Mandy Langfield about the challenges the company faces when it seeks aviation certification for its products
In 2012, when Transport Canada grounded existing HEC equipment, Jeff, along with Derek Thomas, co-founded Boost Human External Cargo (HEC) Systems Inc. Working with pilots and engineers, the team developed a Dual Hook HEC System for the Eurocopter AS350/355, Bell 206L, 407, 205/212/412, and McDonnell Douglas MD 500. Their systems are fully approved by Transport Canada Civil Aviation (TCCA), the Civil Aviation Administration of China (CAAC), Federal Aviation Administration (FAA), and approval from the European Aviation Safety Agency (EASA) is near completion.
“When we started the company, we envisioned that what we would be doing was tweaking existing products,” said Jeff, “but the reality is that the amount of engineering needed for each aircraft/system combination is immense, and really, it needs to be done from scratch for each one.” The investment in engineering each part specifically means that the company is building up a substantial database for each kind of helicopter for which it makes hooks and Personnel Carrying Device Systems (PCDS), and this can be used to enhance projects in the future. “It’s all about continuous improvement and development.”
And it was a bit of a baptism of fire as well. The first aircraft the Boost team worked on were the AS350 and AS355. Finding a Transport Canada (TC) design approval representative (DAR) that understood HEC operations was the first challenge, and they had to find a DAR who was experienced in this world.

The first engineer on the project estimated it would take between three and six months, and cost around CA$50,000. Perhaps it’s not a great shock to learn that this was – to put it generously – an underestimate. Three years, and almost a million dollars later, the company received its Supplemental Type Certificate from TC.
The certification process is a series of known unknowns – in the beginning, the engineers couldn’t be accurate in their predictions. Now, though, the company’s experience and databank mean it is possible to predict with more accuracy how long it will take to certify a product for use in an aircraft. “You can almost say that we’ve developed a recipe for approvals,” said Jeff. “The majority go straight through to TC and are then validated by the FAA and EASA thanks to bilateral agreements between the organizations.” China – for obvious reasons – is less straightforward. Boost works with a local company in China that facilitates the approvals process with the CAAC, and although it isn’t a cheap way of doing it, it is worth the investment.
Obtaining certification for products at home, though, isn’t always easy. TC is run on a regional basis, and while one region might certify a product, another won’t. “There was one occasion,” recalls Jeff, “where TC said to us: ‘no more belly band operations for HEC’. OK, great, we thought, everyone will now have to move to dual hook ops. And then the Prairie Northern region of TC approved a new belly band for HEC operations. It was confusing.”

The aforementioned bilateral agreements can sometimes be a cause for delays and confusion as well, despite the aim of simplifying the process. What one agency will approve without too many questions could cause a lot of issues for another. And because the process involves the information going from regulator to regulator, if the first one hasn’t asked a particular question of the manufacturer that the second one wants the answer to, then the delays between questions being asked and the information being obtained from the OEM can be substantial.
“It’s certainly not a simple process,” said Jeff, “and one that can result in hefty delays for the operators buying these systems.” He cites the case of the Austrian Police Force buying Airbus Helicopters H125s with Boost’s dual hook system. Airbus delivered two such systems three years ago. Approval from EASA is still pending. “The system is used around the world, and has flown thousands of hours,” Jeff continued, “but EASA still has questions to which they need answers.” Resilience and determination are the only things keeping the process afloat at this point! Boost bought its own AS350 B2 and AS350 BA airframe and has performed innumerable tests on it to give evidence to EASA that its dual hook system works and does so safely: “EASA needs data, so we collect it.”

But what does it take to develop a product for certification?
Well, really, it depends on why you’re developing it, explained Jeff. Most products Boost makes are for the rescue sector, but not all. Its latest one is actually for the utility sector – namely, power line workers. The harnesses and lines the company makes for rescue operators is now far outstripped by the utility companies. Boost’s next-generation power lines are enhancing the safety of the workers due to their solid urethane coating, which is see-through. The coating means they are insulated, while the transparency means that the lines can still be checked for quality. Following rigorous and thorough electrical testing for energized HEC operations, they have been approved by TC and the FAA.
The whole process took three years to get the initial approval on the Bell 212/412 and now they are continually being added to all new dual hook systems as they become available. This allows them to be used on almost any helicopter performing HEC operations in North America and around the world.
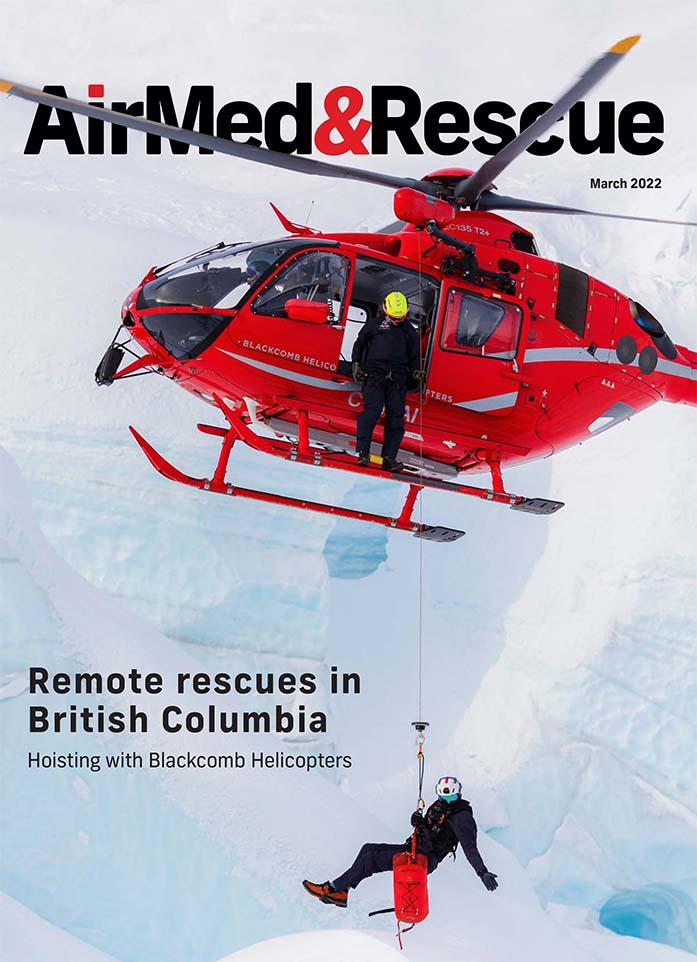
March 2022
Issue
In this issue - international requirements for rescue swimmers, aerial firefighting assets in Australia, flying in icing conditions, and how to maximize the training opportunities offered by VR technology.
Mandy Langfield
Mandy Langfield is Director of Publishing for Voyageur Publishing & Events. She was Editor of AirMed&Rescue from December 2017 until April 2021. Her favourite helicopter is the Chinook, having grown up near an RAF training ground!