MRO software solutions for airborne special missions
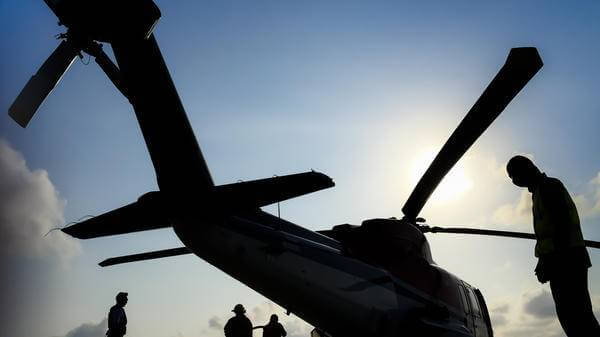
Maintenance, Repair and Overhaul (MRO) software solutions are changing the game for maintenance crews, with digital platforms offering increased efficiency and accuracy. James Paul Wallis identifies market trends from developers and end users
Thousands of individual parts have to work together to keep a helicopter pilot and crew in the air; thus, the staff that look after helicopters take a highly systematic and pro-active approach to maintenance and repair. For example, many parts are replaced when they reach a service life limit, and this has to be scheduled well in advance of any likely failure. In the past, record keeping and scheduling all had to be done using paper. Thankfully, software is now available that simplifies the process, allowing staff to stop chasing paper and get on with maintaining the aircraft. This software can eliminate bureaucracy and automates processes, helping to anticipate and prevent problems, said Steven Cespedes, Head of Aviation for Ideagen, developers of the Q-Pulse software.
through using the right piece of software, we can have an efficient movement of data between our three main MRO functions; parts and logistics, airworthiness and service delivery on the hangar floor
Adam Clegg, Manager of Engineering Operations, Royal Flying Doctor Service (Queensland Section), spoke to AirMed&Rescue about the need for software that can make the maintenance process more efficient. He explained: “Our aircraft cover a lot of miles, but those miles can be very ad hoc. One week an aircraft could fly 40 hours, and the next week it could fly two hours. This can make it extremely difficult to predict maintenance windows for that aircraft. And that is just one aircraft out of a fleet of 20. We also face the challenge of inspections of the medical fit out of our aircraft. These are obviously crucial to our business; however, they can interrupt maintenance schedules. Our goal in addressing these issues is to get to a stage where, through using the right piece of software, we can have an efficient movement of data between our three main MRO functions; parts and logistics, airworthiness and service delivery on the hangar floor.”

Introduction of digital solutions
Although Hospital Wing was billed as the first helicopter air ambulance provider in the US to go fully paperless as recently as 2018 (see side bar below), software aimed at the MRO sector has been on the available for some time.
Flightdocs (Hospital Wing’s MRO software provider), offers its Enterprise system, which combines maintenance, inventory and flight operations into one integrated platform. Lee Brewster, Director of Product Marketing, said that since 2003, the company has been developing software solutions for the aviation industry, adding: “The 2017 introduction of HMX was in direct response to the unique needs of tracking both rotorcraft maintenance and usage. These tools took flight departments from the era of hard copies and spreadsheets to the modern world of cloud-based applications and mobile accessibility.”
the industry has highly specialised practices in areas such as configuration management, maintenance programme, certifications and task signoffs, quality assurance, compliance reporting, reliability analysis
Software provider Ramco entered the aviation sector in the 1990s with its Enterprise Asset Management (EAM) offering, with orders from companies such as Columbia Helicopters. Sam Jacob, Vice-President and SBU Head – Aviation Solution at Ramco Systems, said: “While addressing the needs of the early set of customers, we realised that a generic EAM solution was not able to address the unique needs of aviation maintenance.
Apart from terminology,the industry has highly specialised practices in areas such as configuration management, maintenance programme, certifications and task signoffs, quality assurance, compliance reporting, reliability analysis etc.” The big breakthrough came in 2003, said Jacob, when ‘a large rotor-wing operator in the US’ chose Ramco for its maintenance needs: “The large and complex nature of the implementation which covered bases around the world with over 800 users and over 200 aircraft set the base for future growth in the rotor segment.”
Rusada entered the aviation sector even earlier, releasing its first MRO software back in 1987. Ian Kent, Product Manager, said of the first version: “[It] was a DOS-based solution developed for a single customer. The product quickly caught on, and as our customer base started to grow, we released RAL Professional in 1990, and then ENVISION in 1993. This built upon the success of our first two products and contained a significantly enhanced user-interface along with an array of extra functionality.”
Accuracy and efficiency
LTB400 Aviation Software has customers including DRF Luftrettung. Maximilian Schmitt, Business Development, described how the company’s LTB/400 Maintenance Management System covers all functions of a Part-145 organisation including CAMO (continuing airworthiness management organisation) and flight operations modules. He said: “With our CAMO modules, you are able to track the complete aircraft/helicopter with all the components, LLP and inspections (including findings, AD&SB, etc.). With the maintenance modules, you can directly create a work order out of the due list (from the CAMO section) and you can work paperless via a digital job card.”
Ornge, the provider of air ambulance and related services for the Canadian province of Ontario, has been using Ramco aviation software for its MRO platform since 2012. The advantages of a digital system over paper are many, explained James MacDonald, Ornge Director of Communications and Public Affairs: “The use of paper and spreadsheets leaves room for human error, particularly as information is transposed from one document to another. Ramco provides us real-time visibility on maintenance activities – essentially, a live picture of what equipment, what’s being done and where. It improves efficiency from both a materials and reporting perspective, ensuring all of the maintenance is done on time and as required.”
When maintenance was paper based, added Kent of Rusada, documentation tended to be out of date, so engineers and maintenance staff were not always working with accurate information: “For example, technical logs and completed work packs could often take days, if not weeks, to process. MRO software solutions have enabled organisations to improve on this, but the use of paper is still very prevalent in maintenance operations today, particularly when it comes to issuing work instructions and recording and certifying work carried out. The latest release of ENVISION enables true paperless operations by addressing the certification issues that have long been a barrier to digital MRO.”
Software eliminates duplication of records and effort, said Ideagen’s Cespedes. He added: “Paper-based maintenance would have been done using spreadsheets and physical word documents saved in filing cabinets and electronic folders. This presented a number of issues, mainly around the lack of control of processes and difficulties in maintaining records and achieving and maintaining compliance.” The difficulty of getting your hands on essential management information is a key drawback to paper-based systems, continued Cespedes: “You need to go looking in three or four different places to get information. There are often references and signposts, but not the actual information, so you end up following a paper trail. The same information can be stored in different places with minor variations and the overall picture is fuzzy and liable to misinterpretation. This can lead to wasting time, missing opportunities to do something important, low performance and risk. Sometimes you can’t get the information you need to go ahead with something: wasted opportunities. Sometimes you misinterpret and go ahead at risk.”

Memphis-based Hospital Wing first implemented the HMX software platform in 2016. Lee Brewster is Director of Product Marketing at Flightdocs, which provides cloud-based aircraft maintenance and inventory management software. Brewster said that in June 2018, the air ambulance company became the first helicopter emergency medical service (HEMS) operator in the US to take its operation fully paperless. Using digital rather than paper forms and reports has afforded the organisation increased efficiency across its maintenance and operational processes, said Brewster.
Formerly, Hospital Wing’s team of 12 full-time technicians largely used handwritten logbook entries and spreadsheets for maintenance tracking, work orders, and discrepancy reporting. According to Nick King, Hospital Wing Director of Maintenance, more and more time was being taken up with completing this documentation, and the documents couldn’t easily be accessed by pilots and technicians for reference. Now, paper log books, flight logs and aircraft maintenance logs have all been replaced with the digital system.
As an example, a Work Orders module allows technicians to fill out work orders using quick navigational functions and filters. Helicopter Wing Aircraft Maintenance Lead Josh Wexler explained: “We can navigate the system and cherry pick items from drop-down menus and incorporate into a work order. We view estimated and actual work hours to produce reports based on labour, part and additional cost projections. It’s very effective and easy to use – basically point and click.”

Thus, the ability for multiple personnel to access the same data is a major plus for digital systems, said Jeff Shearer, a licensed helicopter mechanic and Chief Engineer for a rescue helicopter operator in new Zealand. He developed aircraft maintenance tracking and scheduling software Flightcert predominately so that pilots can always know the airworthiness of their aircraft, he explained, adding: “Maintenance tasks comprising of inspections, part replacements, airworthiness directives and service bulletins are tracked by various parameters, such as airframe hours, engine hours, airworthiness directives, service bulletins, landings, hoist cycles and engine cycles to ensure continued airworthiness of your aircraft. These are all tracked and notified to users through both software flags and emails as required.” By being cloud-based, the Flightcert system makes data easily accessible to any user (controlled to access rights and viewing permissions granted by the system administrator), whether pilots, engineers and administration personnel.
LTB has seen the popularity of its LTB400 Aviation Software grow consistently since the company was founded in 1984, said Maximilian Schmitt. “LTB’s system allows users to work ‘in-time’ and cost [effectively]. Furthermore, we shorten the ground time enormously and ensure that the aircraft is back in the air as quickly as possible,” he told AirMed&Rescue. Like Flightcert, LTB’s system facilitates information sharing across departments.
LTB’s system facilitates information sharing across departments
MRO Insider is a web-based resource that allows operators to issue requests for aircraft maintenance and upgrade needs and receive quotes from multiple facilities. For Lindsay Nixon, President of the service, the key benefit of going paperless is efficiency. He said: “The digitalisation of all of this technology and trends have had a significant impact on efficiency. Given the mechanic shortage, the MRO industry needs efficiency more than ever. By adapting to new methods and processes that incorporate these technological advancements, MROs have a great opportunity to streamline their operation and work smarter with the resources they have.”

Human input
Ultimately, the software still relies (to a certain degree) upon humans to input accurate data, so correct training of staff is absolutely essential. Kyle Vergeer, Managing Director at WinAir, believes that MRO software companies must offer a variety of training options based on the client’s particular needs. He explained: “Training should be available as classroom-based training either at their facility or the customer’s, online instructor-led training, and on-demand Learning Management System (LMS) video tutorials. Training must be facilitated during the product implementation phase and be available on an ongoing basis. In addition, comprehensive online help should be available for all users.”
Going from paper to cloud-based doesn’t come without its risks, and again, humans are a part of this risk, in the form of data security. Vergeer told AirMed&Rescue that this risk is mitigated through a ‘robust back-end structure’, while WinAir, through the company’s MRO software, supports the latest web browsers and most recent versions of Java and Microsoft SQL Server. He added: “We utilize data transport encryption with support for the latest TLS/SSL versions and encryption ciphers to ensure data integrity. We also use password management and external directory integration to safeguard against unwanted intrusions.”
We are currently developing a suite of native mobile apps featuring offline capability
Miles to go
Looking at future developments, LTB is working on aspects including an improved user interface. Schmitt revealed that the ‘next generation’ of the software is being planned, but no details are being released as yet.
Over at Ornge, a project is underway to integrate the organisation’s currently separate digital systems, said MacDonald: “We are presently working on integrating the Ramco technology with our dispatch software, FlightVector, to further improve efficiency. For example, at present our aircraft maintenance engineers need to enter flight-related data into Ramco at the start of each day covering our aircraft activity over the previous 24 hours. Once the integration of these two platforms is complete, this information will be pushed automatically from one system to the other. This will allow us to constantly monitor the progress of when things are coming due, and will reduce data entry time on task for the AMEs.”
Meanwhile, Rusada is working on solutions that work offline. Ian Kent said: “We are currently developing a suite of native mobile apps featuring offline capability.
This will allow users to continue working without an internet connection, dramatically reducing the time it takes to complete tasks.” The first such app to be released is designed for engineers, allowing them to perform day-to-day tasks without being tied to a PC.
The next step for Ramco could be to remove the need to manually enter data. Jacob said: “Ramco’s aviation roadmap is laid out to achieve zero data entry by extensively leveraging the capabilities of artificial

intelligence/machine learning. Ramco’s Voice as a new UI project leverages devices like Google Home and Alexa, enabling users to perform tasks through voice conversations. Current capabilities allow users to perform various tasks ranging from stock enquiry to approvals. We are continuously working with our customers to improve the effectiveness in busy noise-prone shop floor environments.” Another area of focus at Ramco is on building the APIs to seamlessly connect with any third-party systems including Original Equipment Manufacturers (OEMs), part suppliers and shipping agencies, said Jacob.
Overall, Nixon of MRO Insider predicts that the general MRO industry will become even less paper-based and more digital going forward: “The MRO industry as a whole is just beginning to shy away from paper. A great example is through maintenance quoting. Instead of calling around and getting paper quotes for maintenance, they can complete that entire process online. The use of blockchain in aviation maintenance is starting to gain traction as well for improved tracking and monitoring of parts and components. The simple habit of using computer programs or CRM software to track customer information, keep up-to-date records between shifts and departments in an MRO setting is great for customer service and customer experience.
The simple habit of using computer programs or CRM software to track customer information, keep up-to-date records between shifts and departments in an MRO setting is great for customer service and customer experience
The use of technology on the shop floor itself is improving as well – allowing technicians to scan in and out of jobs, scanning tool and part inventory, and using all of that information to create invoices for customers. Within the last decade, the quality of technology available to MROs has improved significantly.”
Vergeer of WinAir pointed out that while there are doubtless many safety benefits of going paperless, there remains work to be done with system integration: “Aviation operations can actively integrate their maintenance software with any third-party flight-ops system to provide dispatch information. They can also expand this paperless approach to other areas of their operation to allow for greater situational awareness with respect to aircraft maintenance. By integrating all aviation maintenance processes into comprehensive and robust aviation management software, operations will gain from total transparency between departments and easy access to trustworthy data.”
Todd Lewis, President for Component Control, shared with AirMed&Rescue the ways in which the company is supporting a paperless environment.
Quantum Control, developed by Component Control, provides several modules and related functions designed to support a paperless MRO environment, including Document Imaging, Mobile Imaging and Mobile Technician modules, which Android, IOS and browser technologies support. As an ERP software provider and integrator, it’s important to provide your customers with an implementation methodology that allows for the adoption of new processes and efficient workflow, while maintaining the regulatory compliance issues legacy systems were designed to address. In our experience, it’s less about incorporating legacy systems than it is demonstrating the time saving aspects, increased data accuracy and better adherence to regulatory compliance.
Although Component Control has deployed Quantum Control at over 1,600 aviation companies in more than 65 countries around the globe, we find there is a lot of commonality in processes due to the highly regulated nature of our industry, though each region and customer has unique requirements that need to be addressed. To facilitate a streamlined and lean implementation process, Quantum Control is designed to be highly configurable, scalable, and support a variety of deployment options i.e. Hosted, Cloud Based or On-Premises.
Quantum Control is designed to support Aviation best practice out of the box, which limits the items that need to be customized during the implementation to the user interface, integrated dashboards, and system outputs such as forms and reports. Quantum Control has been designed to provide the tools for our customers to make these changes though we also maintain a full staff of developers, data analysts, and trainers to design, develop and implement our applications in an efficient manner.
For further information visit www.componentcontrol.com

Jorleif Bech, Founder of MRO software provider Lundin, spoke to AirMed&Rescue about the need for collaboration in the industry if a truly paperless goal is to be achieved.
We have a few customers that have already removed the paper from the day to day routines in the hangar. This means that all work is done digitally and then paper can be generated when all work is done, and if needed – a final signature can be added to satisfy classic requirements.
For customers to go fully paperless, we need to work with other providers. For example, we integrate with electronic flight bag (EFB) systems to receive flight information and to give back information on aircraft status so that the EFB can show next due maintenance, open MEL’s and such.
With each aircraft operator being unique, it is important to offer customizable options to customers, and this is achievable mostly by configuration options. This is to accomodate not only differences in operation, but also differences in the type of fleet the customer operates. The part where we usually do the most customization is in reporting and in integration with other systems that the customer is using, whether this is linking to EFBs, flight planning, intranet, finance or other information systems that are being used.

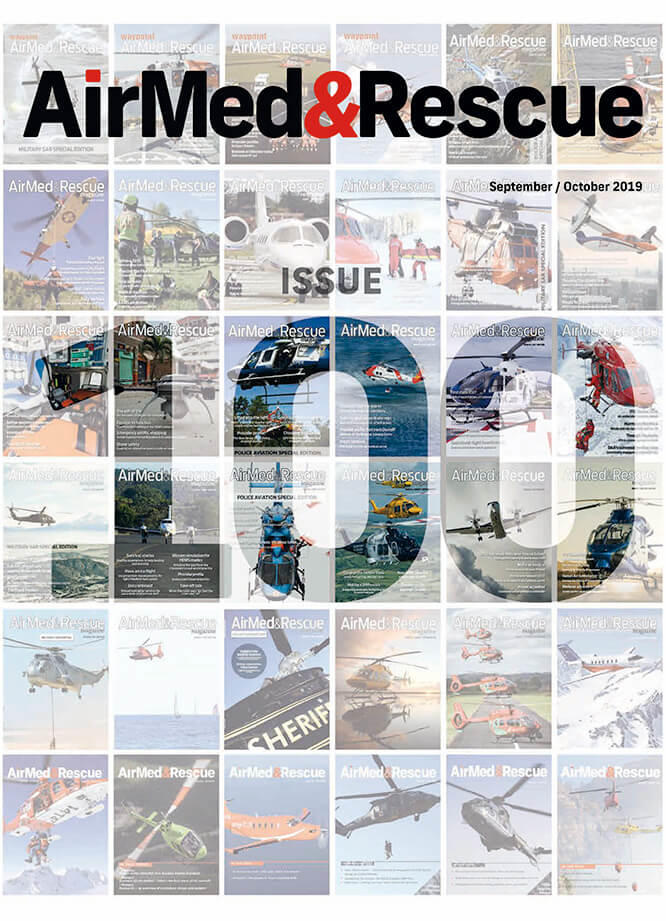
September 2019
Issue
In this issue:
When the lights go out: The challenge of nighttime rescues
Digital dream: MRO software solutions
Interview: Samir Mehta, President of Collins Aerospace’s Mechanical Systems
Case Study: TrustAir reports on a neonatal mission
Industry Voices:
- ICAO Annex 14 amendment – is your helipad ready?
- The cost of reimbursement of emergency medical flights in the US
Special report: Blood delivery by zipline
Med Insight: Airway management training
James Paul Wallis
Previously editor of AirMed & Rescue Magazine from launch up till issue 87, James Paul Wallis continues to write on air medical matters. He also contributes to AMR sister publication the International Travel & Health Insurance Journal.