Innovation for all: latest advancements in SAR equipment
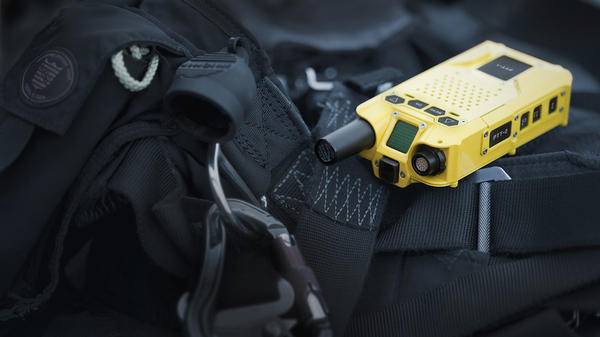
Dr Joetey Attariwala explores some of the latest advances in SAR equipment that pair innovation with affordability
There are a myriad of advancements in SAR technologies around the world. Some are innovative new approaches to time tested capabilities, while others are evolutions of existing equipment. SAR operators keenly follow such advancements but readily acknowledge that cost of equipment is often a barrier to entry, particularly for smaller operators.
Rob Munday of SR3 Rescue Concepts, stated: “There is no doubt that new technologies help facilitate SAR missions and that they can make things safer. With that said, new technologies also come with a cost, so when the vast majority of SAR providers work on limited budgets, there must be strong consideration on the acquisition of new kit versus spending the same money on good training so that every mission is always conducted safely.”
New technology to stabilize stretchers
While the uncontrolled rotation of hoisted stretchers is a common problem often resolved using a tag line, there are situations where its use is insufficient or impractical. To resolve this, some companies have developed stretchers which have been modified with aerodynamic rudders for greater stabilization.
Vita Inclinata, headquartered in Colorado, US, saw a market for a lightweight load stability system that could attach to any rescue kit, be it Stokes litter baskets, Skedco stretchers, or rescue bags. The resulting Vita Rescue System weighs 40-50 pounds and can collapse into a small, compact, and lightweight unit, and employs electric propulsion impeller fans and smart software to stabilize the load of any rescue kit configuration from unwanted swing or spin. The system acts as an active dampening solution where the stabilization time varies based on cable length, patient weight, and environmental disturbances. According to Vita, a typical swing stabilization for an empty rescue kit is 1.5 swing periods.
“One of the benefits of our Vita Rescue System is the ability to fly-to-target,” said Caleb Carr, CEO of Vita Inclinata. “What we’ve done is de-couple the load stability from the aircraft. That means we can stabilize the rescue basket, but we can also fly the hoist to a location, off axis, like to a cliff side, which we might not otherwise be able to reach due to the helicopter’s rotor blades. This completely revolutionizes the way helicopter SAR is done.”
Derek Sikora, Executive Vice President of Engineering and Chief Technology Officer at Vita Inclinata, added: “A typical hoist rescue with our Vita Rescue System takes about two minutes. Our tests have demonstrated that we are adding time to the ‘Golden Hour’ for patients, we’re expanding the operational capacity of the helicopter because we are significantly reducing the amount of hover time on site, and most importantly, we’re eliminating injuries or death that results from the use of tag lines.”
A Vita Rescue System unit was recently acquired by Two Bear Air Rescue in Montana, US, and is expected to be delivered within the year. On the military side, Congress appropriated US$5.5 million to the US Army for provision of the Vita Rescue System for National Guard Units in Montana and South Carolina, and to active duty Army units of the 16th Combat Aviation Brigade in Washington State, and the 25th Combat Aviation Brigade in Hawaii.

New Rescue Hoist design
Very few changes have been made to the general design of hoists over the past 50 years. The most significant the industry experienced was in 1999 when the FAA made changes to part 27 and 29 rules for Human External Cargo. But today, the industry is now preparing for some of the most significant changes since, as the FAA will soon adopt new rules developed by helicopter and hoist manufacturers to improve safety and meet the evolving requirements of hoist operators and regulators.
To meet these new requirements, Collins Aerospace’s Goodrich team has been engineering a new hoist called Pegasus that will provide operators with improvements in both functionality and maintenance. “We first went to our customers – helicopter manufacturers and operators – big, small, civilian, military,” said Nick Demogines, Business Development Director, Hoist & Winch for Collins Aerospace. “We asked them what they needed and wanted in a hoist. We received nearly 5,000 individual responses and Pegasus incorporates nearly all of their ideas.”
Collins engineers took the opportunity to start fresh, reimagining and improving on nearly every aspect of hoist operation and maintenance. Pegasus will simplify maintenance by removing the need for specialized tools, incorporating a lighter and more ergonomic control pendant, and simplifying integration into the rotorcraft. Some key features of current Goodrich hoists, such as the translating drum architecture that enables a single point payout, were also improved upon.
Some changes will be more immediately apparent to operators, such as the slightly larger diameter hoist cable, while others will be more discreet, such as a new planetary gearbox with overload clutch and brake.

To avoid an aircraft on ground situation due to a hoist malfunction, the Collins team developed the Pegasus’ major assemblies like the motor, controller, and gearbox to be modular, so they can be swapped out without removing the hoist from the rotorcraft. This saves the operator a potentially time-consuming and expensive return to the manufacturer for repair.
Considerable time and money has been spent across the industry to increase cable life, less frequently birdcage, avoid mis-wrap, and still be simple and fast to replace if they are damaged during a rescue. Collins reviewed the hoist cable as a critical component during the development of Pegasus. With Pegasus, the hoist operator will see more data on the control pendant – in addition to cable length, there is hook load, and more information on hoist status is provided as well, all of which is leveraged by Pegasus’ new digital backbone that also ensures mission data will be available for download and analysis or integration with the aircraft Health and Usage Monitoring System (HUMS) system.
Collins is currently working through ongoing testing of Pegasus and navigating regulatory requirements as the FAA needs to formally adopt SAE AS6342, with EASA guidance still forthcoming.
Centum details how its Lifeseeker airborne system locates cell phones and how it supports the Canadian Royal Air Force SAR operations - sponsored content
Centum was granted the CASSAR contract by the Canadian Department of National Defence (DND). What were the parameters the DND were looking to fulfil?
The DND was looking for a Cellular Airborne Sensor for Search and Rescue (CASSAR) system for Royal Canadian Air Force (RCAF) SAR operators, since they didn’t have any capability to locate cell phones associated with people from an aircraft.
Key requirements are a minimum reach of 20 km, automatic scanning of local networks or placing a two-way voice call, and text message functionality. To ensure privacy, the technology should restrict the search to ‘phones of interest’ only. Optional requirements that Lifeseeker also met include requesting and receiving GPS coordinates from a phone of interest or detecting and tracking multiple cell phones.
Since the CASSAR system is also to be used in Disaster Relief operations, other key functions to fulfil including broadcasting public safety text messages such as warnings and directions to victims and providing mass mapping capabilities in areas with little-to-no cellular infrastructure.
The Lifeseeker is currently installed in the RCAF Hercules C-130. What other aircraft will the Lifeseeker system be compatible with in the future?
Lifeseeker has the DO-160 qualification, a standard adopted by all major aerospace and avionics manufacturers that defines environmental test conditions and procedures and criteria for avionic equipment. As such, Lifeseeker can be integrated into any aircraft, but the installation of any airborne sensor must be certified by an authorized organization in accordance to thier guidance.
A recent example of this has been the EASA Supplemental Type Certificate (STC) launched by AKKA Technologies for Lifeseeker on AS332 Super Puma, the aircraft model that CHC Helicopters will be operating in Tromso. Norway for SAR missions. Ultimately, Lifeseeker is capable of being integrated into any aerial platform.

Preventing Dynamic Rollout on hoist hooks
Dynamic Rollout, also know as ring rollout, can occur when rescuers are hooked up to certain hoist hooks. Under certain circumstances, their ring can roll around the beak of the hook, which could result in detachment from the hook and lead to significant injury or death.
To resolve this issue, Lifesaving Systems Corporation (LSC) has designed the D-LOK Hoist Hook which eliminates all problems associated with current double rescue hooks, such as inadvertent engagement, including the snagging of fingers on the small hook, and self-release or ring rollout.
Another problem for rescue helicopter operators is when rescuers get snagged while the cable is on load. The only resolution for such a scenario, until now, was to cut the cable.
The company’s new D-LOK hoist hook is a positive locking hook which extends the latch guards to fully enclose the actuation buttons and adds a radius to the face of the hook gate. According to Mario Vittone, General Manager at LSC, the extended latch buttons and raised guards improves the users control of the gate during one-handed operation. The hoist hook features a large ring volume for multiple equipment rings, and will accept rings up to 3/4-inch diameter. The hook also has an integral utility eye which allows for attachment of a tag or guide line.
“Our new D-LOK has a different shape of the gate, so we have re-patented it, and we have a new patent on the way the buttons are guarded too,” explained Vittone. “The US Army is the launch customer for the new D-LOK.”
Another problem for rescue helicopter operators is when rescuers get snagged while the cable is on load. The only resolution for such a scenario, until now, was to cut the cable. LSC recognized this problem and recently developed the Quad-LOK Release, the first purpose-built device intended for helicopter hoisting operations designed to release under loads over 200 kilograms, and is ambidextrous in operation. The Quad-LOK Release was approved by the FAA in March and is currently only approved for integration with the TRITON II Harness. The device is integrated on the riser hoist strap, which is easily accessible to the user, and allows for quick egress from the harness in the event of an emergency.
“The Quad-LOK Release meets all requirements to be light, and be able to release under high, unpredictable loads,” explained Vittone. “The double locking cover, and a double locking main release are designed to be operated single handedly. Our system is the only one that allows you to open the lock, and if the situation changes, close it back again.”
With an order of 100 units, the Royal Australian Navy is the launch customer for the Quad-LOK Release.

Avē CASSAR
Sensor capacity like CASSAR can deliver a new generation of SAR capability to existing platforms, and the Royal Canadian Air Force (RCAF) is seeking to introduce a new generation capability with the Cellular Airborne Sensor for SAR (CASSAR). This standalone piece of equipment can be loaded on all RCAF SAR aircraft, including fixed-wing aircraft like the Kingfisher. The system will function like a cellular tower and will allow the RCAF to track a cell phone for SAR.
“This system will be able to detect a cell phone signal which is important in the connected world that we live in today,” said LTG Meinzinger. “The ability to very rapidly home in on a cell phone is going to be a significant game changer for the search and rescue crews.
“The CESSAR contract was awarded to [Centum’s] Lifeseeker in March 2021 and will be an off-the-shelf capability that is currently being used to great effect by other nations including Norway. It’s a critical capability as you can imagine and has the potential to dramatically assist the search phase of SAR operations.”

Wireless, encrypted talk
Headquartered in Norway, Axnes has been developing and manufacturing these mission critical wireless intercom systems optimized for SAR teams of the North Atlantic and North Sea, as well as other harsh environments around the globe, for 26 years.
Their newest product is the Polycon Next Generation (PNG) wireless ICS extension, a highly adaptable, encrypted, full duplex mission system that extends communications beyond an airframe at a robust line-of-sight range. The PNG can be connected to platform installed radios, allowing users to access radios from a remote position and to communicate through platform installed radios such as Satcom, C2IS, or TETRA. Intercom loops may also be created in the wireless domain, allowing teams to interact or work independently when required, and for team leaders to broadcast across teams.
The PNG handheld transceivers — MP30 and MP50 — include a GPS receiver allowing the position of the outside crew to be monitored on mission displays; transmission of this position information is done in secure mode. PNG handsets have a battery time of 15 hours operation, and 40 hours on standby. The models can be mixed within the same system and there is no limitation to the number of units connected. Another highly useful feature is the remote activation of the AIS-SART frequency installed in the amphibious MP50 model, should the swimmer become incapacitated.

Axnes’ David Betts relayed an incident while he was working with CHC, which runs the Irish Coast Guard’s all-weather SAR helicopters. Betts was carrying out a night hoist to an oil rig support vessel which was 90 miles off the coast of Ireland: “We were conducting a 180-foot hoist in 45 knots of wind and 6 metre seas, with a hi-line established. I was 20 feet from landing on the vessel when the aircraft experienced a BIM warning [system to warn of low pressure inside the main rotor blade spars] with an audible alert. Thanks to the Axnes system, I was able to hear the alert, and hear the co-pilot say I should get onboard, to which I immediately gave a thumbs up to the winch operator. At one point, the pilot said he would like to get some airflow through the disk and if I was happy if he moved off. I simply gave a thumbs up to the winch operator. As the situation unfolded, I remained completely situationally aware of what was occurring, and I feel that’s a great example of how the Axnes PNG truly is a next generation Search and Rescue technology which is available today.”
According to Axnes, the PNG system can be retrofitted and configured to work with any existing ICS or helmet/headset combination and is designed to qualify for all relevant aerial, maritime and ground vehicle platforms, both civilian and military.

October 2021
Issue
- The demand for automation reveals its shortcomings meeting the human factor
- How virtual and augmented reality meets the needs of SAR/HEMS training
- Keeping critical communications infrastructure live during Hurricane Ida
- How logistics is the critical challenge of neonatal air transport
- The latest SAR equipment that pairs innovation with affordability
- Interview with Rob Pennel about the EASA South East Asia Partnership Program
- And more
Dr Joetey Attariwala
Dr Attariwala trained as a medical doctor and has established himself as a highly regarded journalist who contributes to various aerospace, defense, training and simulation, and law enforcement publications around the world. He is a regular contributor to AirMed&Rescue magazine.