Helipads in the 21st Century
Where and how helicopters are being used as air ambulances is shifting, and in an increasingly urban environment, new designs and stricter safety protocols are changing the helipad game. Mandy Langfield spoke to industry experts to find out more about how helipads are being modified and improved for the air medical sector
Helipads, helidecks, heliports – from the traditional steel and concrete structure embedded in the ground, to helidecks onboard oil and gas platforms made from aluminium, and even matting products that can be rolled out onto soft or unstable surfaces to give helicopters a safe place to land, the wide variety of technologies employed in the design of helipads continues to evolve to promote safer environments for pilots, crew and aircraft.
Changing demands
Hospitals around the world are adding helipads in their grounds, or on top of their Accident & Emergency departments. The fast reactions of helicopter emergency medical services (HEMS) to pick up a patient from their location has to be followed by immediate access to the doctors on arrival at a hospital, so the location of the helipad is carefully thought through in order to ensure optimum speed to treatment. It is no small investment either, with many hospital helipads costing in excess of GB£5 million. The difference it can make to patients, however, is undeniable. Luton and Dunstable University Hospital in the UK, for instance, is currently saving for the construction of a helipad. Chairman of the hospital Simon Linnet said: “This helipad will provide a life-changing facility for our community which will link directly into the centre of our leading emergency department.” The funding for the pad is being raised in part by the HELP Appeal – Helicopter Emergency Landing Pads is a charity dedicated to (as the name suggests) funding helipads for hospitals around the UK. Robert Bertram, Chief Executive of the HELP Appeal, added: “This helipad will allow the East Anglian Air Ambulance and other air ambulances to land a critically ill patient on site, where he or she can be transferred comfortably and smoothly to a consultant’s care within a matter of minutes. This is a must when the slightest jolt or delay by road ambulance could jeopardise their survival.”
Elsewhere, in New Zealand, a new helipad for the South Canterbury District Board is under construction on the site of the hospital’s old administration block, as part of a broader re-development of the emergency department. The move from its previous location at the local Botanic Gardens, according to the hospital’s corporate services director, was driven by the Westpac Rescue Service, which provides air ambulance services to the region. He explained: “We’ve taken onboard what the helicopter operators have been telling us. They would like to see it moved. Fundamentally, it is something we have to do.”

New construction methods
Rocky Allen, Regional Manager in Western US for Bayards, explained why helipads are now being constructed from different materials: “Aluminium offers many advantages over other materials used. We’ve seen the demand for aluminium since the mid-80s when we began building for the offshore market, where this metal performs well in the saline environment. The weight savings, assembly time, and long-term operational cost savings has made it a compelling choice for onshore and offshore construction. Furthermore, there has also been a movement in the construction industry in general towards the use of more sustainable products (aluminium is 100 per cent recyclable without compromising on strength or quality), and helipad manufacturers are no exception to this.”
The increasingly crowded urban environment has also impacted this decision to move to aluminium, explained Allen. With its weight saving qualities, aluminium helidecks can more easily be built on rooftops. Furthermore, in seismic sensitive areas, reducing structural weight of a helipad by 60 per cent may offer more opportunities to incorporate a helipad in the design of a building.
in seismic sensitive areas, reducing structural weight of a helipad by 60 per cent may offer more opportunities to incorporate a helipad in the design of a building.
The US HEMS sector, Allen continued, has been slow to adopt aluminium helipads at ground level.
However, Tom Schuman, President of FEC Heliports, explained to AirMed&Rescue that globally, there has been a ‘significant shift’ over the past 10 years towards the construction of helidecks from aluminium. He went on to explain: “This is more so for rooftop helipads, but we are also seeing the aluminium products being used in ground applications as well. The 6000 series aluminium has many advantages for customers. It is significantly lighter than concrete and has the same strength. The only maintenance required for the aluminium is the repainting of the markings as the aluminium will never breakdown or crack as concrete will do over time. In areas that utilise snowmelt systems in their helideck, the advantages become even more evident. The aluminium design allows the customer to access and maintain the snowmelt tubing as needed versus being encapsulated in the concrete slab.”
The construction of the aluminium design is also much faster and gives contractors more options as to when the helipad can be built in the schedule. Most aluminium helipads can be assembled in three weeks, whereas a concrete helipad will take between four and five weeks to build, and an additional 28 days of curing time, weather depending, so the resources needed are increased.
Schuman also noted that aluminium products are gaining ground in the offshore market, which for years has been dominated by metal. He explained: “The weight advantage of aluminium offshore is becoming more important the farther the oil rigs go offshore to explore. Many of the newer semi-submersible rigs are very dependent on overall weight in the design, as are the support vessels that have landing pads mounted on the bow. For many years, the offshore market was concerned about how the aluminium products would react to fire, but the melting temperature of the aluminium alloys are very high and the fire suppression options have also improved dramatically.”
Fire suppression
Firefighting on a helipad that is 100-feet in the air is a challenge. Foam fire protection is, however, one of ways in which helipads can be defended. compressed air foam systems (CAFS) are fire suppression units that inject compressed air into a foam solution in order to generate a foam that has a tighter and denser bubble structure than water with a standard foam solution. The bubble structure means that the foam can adhere to horizontal and vertical surfaces, while being more effective at tackling the fire as it can penetrate the flames deeper.
According to Burner Fire Control, which manufactures self-contained custom fire suppression equipment to customers’ specifications, the design criteria for CAFS are based on the size of the helicopter(s) using the deck. The company explained in more detail: “International Civil Aviation Organization (ICAO) Section 6.83 states that it is considered essential that firefighting agents are able to be applied to any part of an elevated heliport irrespective of wind direction. The Civil Aviation Authority (CAA) and Federal Aviation Administration (FAA) specifically call out the need for multiple redundant equipment as they state a helicopter accident, which results in a full spillage with wreckage and or fire and smoke, has the capability to render some of the equipment inventory unusable or preclude the use of some passenger escape routes. CAP437, similar to ICAO, states that the operational objective should be to ensure that the system is able to control a helideck fire associated with a crashed helicopter during a range of weather conditions. Section 2.2 states that if a fixed system is in place, consideration should be given to the loss of downwind foam monitors either due to limiting weather conditions or a crash situation. ICAO also states that areas of a helideck and its appendages that may, for any reason, be otherwise inaccessible to fixed monitor systems, it is necessary to provide additional hand-controlled foam branch pipes.”
Deck integrated fire fighting systems (DIFFS) consist of a skid that processes firewater inflow to output foam or water
Deck integrated fire fighting systems (DIFFS) consist of a skid that processes firewater inflow to output foam or water. Nigel Barratt, Vice-President of International Business Development for Marsol Technologies, explained more about DIFFS to AirMed&Rescue: “With the DIFF system, instead of using two or three externally fixed foam discharge monitors (or even just hose reel stations), multiple nozzles (commonly referred to as pop-ups) were developed to be installed on the actual helideck surface,” he said. “When the system is activated – be it by fire and gas sensors or manual remote push-button – the nozzle is then ‘popped up’ by the pressure from the discharging water/foam. Producing a spray pattern that is both horizontal and vertical, the water/foam is then applied right into the heart of the fire, rather than just from the side. This spray of foam/water droplets has the effect of reducing the temperature while the blanket of foam that is formed covers fuel – be it ignited or otherwise – on the surface of the helideck thus suffocating and extinguishing the fire.”
Recent innovation and developments have seen DIFFS further enhanced with the introduction of non-pop-up nozzles, which reduce the issues of malfunction and maintenance as well as removing the risk of being a trip hazard, which could be a severe hindrance during a rescue operation. As with pop-ups, the system is designed based on the specification as laid down by the UK-CAA-CAP-437 standard – meaning the nozzles are tested in various weather conditions to control a fire in less than 30 seconds after system activation.
Corienne Kilgannon, Communications Director for the County Air Ambulance Trust, and the HELP Appeal, added: “DIFFS can put out a fire within 15 seconds, allowing air ambulance crews to continue treating and transferring a critically ill patient to the emergency department as quickly as possible. They can also save hospitals money every year by reducing staffing costs with firefighting teams no longer required to fight a fire. These savings have been allocated to other lifesaving services.” Working with the CAA, Robert Bertram, HELP Appeal Chief Executive, has enabled DIFFS to be installed at Kings College Hospital, St George’s Hospital, Bristol Royal Infirmary, Brighton Hospital and Manchester Royal Infirmary.
Helipads that contain built-in automatic fire suppression systems are allowed a water-only DIFFS, while unperforated steel, concrete and aluminium helipads require the use of aqueous film forming (AFF) foam. Barratt went on to say:
“The majority of foam concentrates used are suitable for Class B hydrocarbon fuel fires and classified by ICAO as Level B or Level C type, with most of the concentrates now being of the C6 formulation as opposed to the earlier C8 type formulation – this being a determination on how well the chemical composition breaks down in the environment.”
At the moment, DIFF technology demonstrates far superior deck coverage than traditional Foam Monitor systems, effectively complying with the NFPA’s requirement to have 95 per cent suppression coverage of a helideck
He continued: “In most parts of the world the disposal of foam concentrates into the water is prohibited and strictly monitored. Therefore, foam producers have developed environmentally sustainable firefighting foam concentrates that effectively extinguish Class B fuel fires with no environmental concerns for persistence, bioaccumulation or toxic breakdown.
While the use of Foam Concentrate plays a very important and crucial role in extinguishing fires, DIFF nozzles are also tested and approved to be used with only water for when installed on helidecks manufactured to a passive fire-retarding construction, i.e. capable of removing significant quantities of unburned fuel from the surface of the helideck in the event of, for instance, a fuel spill from a ruptured aircraft tank.”
Rocky Allen of Bayards ran through some of the advances in fire suppression systems: “At the moment, DIFF technology demonstrates far superior deck coverage than traditional Foam Monitor systems, effectively complying with the NFPA’s requirement to have 95 per cent suppression coverage of a helideck.
Along with integrating state-of-the-art fire-fighting technologies, Bayards’ contributions include the development of the SafeDeck passive fire-fighting system, which further enhances fire safety on the deck by draining the burning liquid and starving the fire of oxygen, thus extinguishing deck fires quicker.”
Innovations
Bayards’ latest development in deck planking consists of a glass blasted surface instead of the former ribbed-serrated surface, giving the deck more friction, making it safer, but also smoother, so patients on stretchers are given a much smoother ride too. Furthermore, it is non-glare, so pilots won’t be blinded by a shiny surface while they are trying to land the helicopter. Another bonus is that there is no paint needed on the planks, significantly reducing maintenance and operational costs for owners, and they are friendlier to the environment.
Other accomplishments by Bayards to improve safety include the development of a handrail that comes with LED lighting integrated into it, keeping crew members safe accessing the helipad and providing aesthetically appealing walkway lighting.
Also on the eco-friendly note, Bayards has developed the first heated eco-friendly helideck for a client in Sweden that does not utilise any foam in its fire suppression system – it is all water. This was demanded by the client, who did not want to use chemicals as part of its firefighting system.
Mobile systems
FEC HEMS-Station® Solar Plus is a mobile system that can be installed and operationally ready within three days. It provides a re-locatable, semi-permanent heliport lighting solution that can be implemented almost anywhere in the world, due to its solar power mains autonomy. The HEMS-Station® Solar Plus houses 10 HEMS-Star® portable lights in an IP65 rated secure cabinet, has VHF, UHF & SMS connectivity, comes with portable LED internally illuminated WDI, resulting in an economical yet fully compliant low visibility/night operational helipad solution.
Helipad matting is another way to create a temporary helipad, utilising a temporary and portable surface deployed on a variety of terrain to aid the safe taking off and landing for all types of helicopters. It improves the safety of landing and take-off by providing a visual flooring area which can be seen from high altitude, but most importantly preventing ‘Brown Out’ – an in-flight restriction of vision due to dust or sand being pushed into the air by the helicopter’s down force. This is particularly dangerous for helicopter pilots as the kick up of dust and sand can cause spatial disorientation and can lead to potential accidents on landing and takeoff.

Standards, rules and regulations
The rules and regulations that govern the construction qualities and maintenance requirements of helipads are wide ranging, and ever changing. Civil aviation authority regulations in individual countries – CAP 437, ICAO annex 14, NMD 072 and NORSOK C004 – are just some of the standards to which helidecks must adhere. Furthermore, different helicopters, with varying performance levels, can affect the size and location of a helipad. In the UK, for example, only Group A/Class 1 performance helicopters are permitted to land at, or take off from, roof-top helipads, and the operator must require a Rule 5 permission from the CAA. The helicopter type intended for use at a helipad must possess a helipad profile for the specific rooftop site within its flight manual. According to the British Helicopter Association, this means that in the event of a failure to one of the power units occurring at any time during the take off or landing, it will enable the aircraft to reject safely onto the available helipad, or to fly away, avoiding all obstacles by a margin of at least 35 feet.
Safety considerations, of course, are at the heart of all standards and regulations, but they are also at the heart of design innovations. As demand for services increases, and more air ambulance helicopters are introduced in urban environments, the enhancements in the design and technology of helipads will no doubt continue apace.
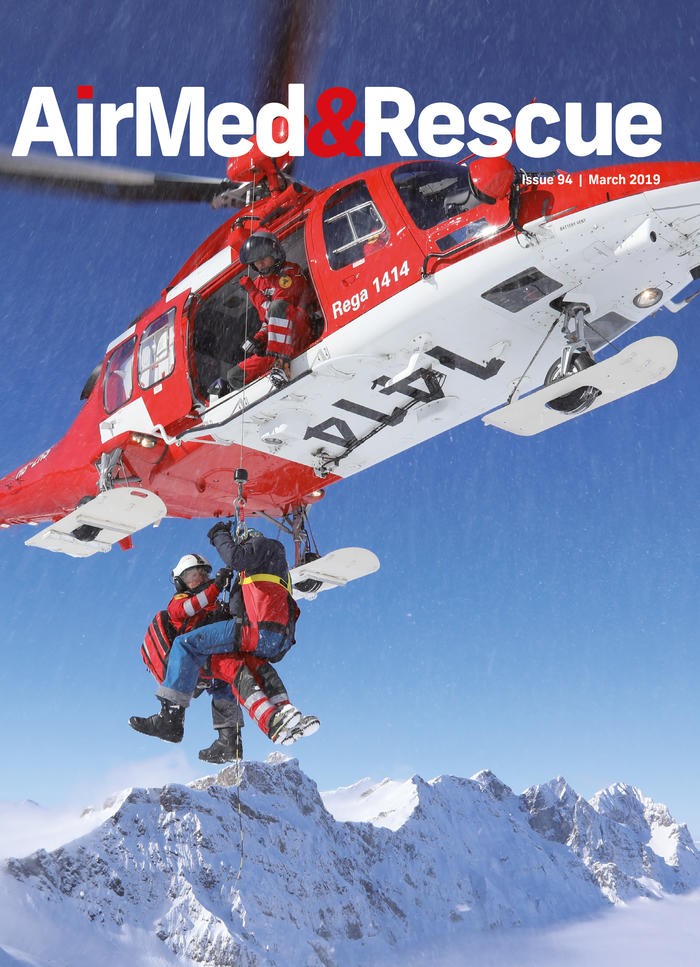
March 2019
Issue
In this issue:
Traumatic brain injury transports - best practice
Survival of the fittest - ALSE - Staying alive after a helicopter crash
Surf's up - Surf-based rescue techniques
Never forget - the lone survivor of a helicopter accident
Patient safety is the number 1 priority for ER24
Interview: Mikko Dahlman, Coptersafety
Provider Profile: LifeFlight Network
Company Profile: Sikorsky / Lockheed Martin
Case Study: AirLec Ambulance describes the challenges of an evacuation from a warzone
Mandy Langfield
Mandy Langfield is Director of Publishing for Voyageur Publishing & Events. She was Editor of AirMed&Rescue from December 2017 until April 2021. Her favourite helicopter is the Chinook, having grown up near an RAF training ground!