Giving old aircraft a new lease of life as aerial firefighters
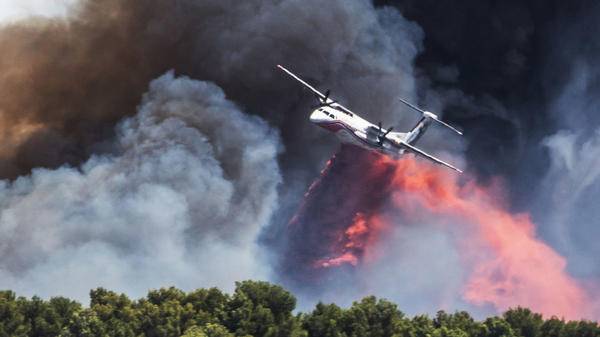
Mandy Langfield explores the breadth of avionic upgrades in use by aerial firefighting operators around the world. From air tanker upgrades to water cannons, each aircraft modification has proven to be a vital in ensuring the success of a mission
New adaptations made to old aircraft ensure longevity and continued use in aerial firefighting fleets around the world. While new aircraft are being built for use in aerial firefighting roles, certification is some years away. Until then, aviators are reliant upon upgrades and adaptations to older aircraft to fight fires from the air. Below is a round-up of some of the most commonly used variants being put to work as aerial firefighting aircraft.
Erickson S-64
The Erickson S-64 Air Crane has been in operation for over 50 years, and has done sterling service throughout that time. The latest generation of the S-64, known as the S-64F+, is expected to be introduced by 2024, and will offer users a multitude of new features and technology.
A company spokesperson told AirMed&Rescue: “Erickson Incorporated is investing in new engines, Sikorsky’s MATRIX™ Technology for fly-by-wire autonomous flights, an enhanced water cannon, and composite main rotor blades. These four investments will revolutionize and modernize this vehicle for the future of aerial missions.”
The new engine will have multiple benefits, including a 30-per-cent fuel cost saving compared to the legacy engine, and improved performance in hot and high environments. The new digital control system – MATRIX – also serves to increase the safety of aerial firefighting operations by enhancing pilot situational awareness, even in reduced visibility, as well as reducing lifecycle and operating costs for users.
The spokesperson commented: “MATRIX™ Technology will increase safety and mission success. Flights that are pilot-optional via fly-by-wire technology will allow for flight in degraded visual environments (DVE) like wind and sandstorms. In military operations, it will also allow for the recovery of unmanned systems and increased cargo transport.” In fact, the aircraft, in an optionally piloted capacity, is now being considered for nighttime aerial firefighting, which will dramatically decrease the loss of life and property in wildfires.
Erickson’s new water cannon can tackle difficult urban high-rise firefighting demands, and will also provide enhanced precision for wildland firefighting. Finally, the new composite rotor blades, which have just been approved by the Federal Aviation Administration, offer an 88-per-cent increase in payload compared to metal blades, and have the capacity to extend aircraft performance.
The De Havilland Canada DHC-8, commonly known as the Dash 8, is a series of turboprop-powered regional airliners, introduced by de Havilland Canada (DHC) in 1984. All Dash 8s delivered from the second quarter of 1996 (including all Series 400s) include the Active Noise and Vibration System designed to reduce cabin noise and vibration levels to nearly those of jet airliners.
To emphasize their quietness, Bombardier renamed the Dash 8 models as the Q-Series turboprops.
Conair manufactures modified RJ85, Q400MR, and Q400AT aircraft for use in aerial firefighting and transporting people/cargo in support of emergency response operations. “Since Conair started, we’ve modified over 15 different aircraft types into airtankers, producing over 150 different aerial firefighters.” says Jeff Berry, Director of Business Development at Conair. The company recognizes that the time has come to modernize fleets, keeping the firetrucks in the sky when the call comes, acknowledging that legacy airtankers are reaching the end of their sustainable life. Conair’s answer to the future of aerial firefighting is the Dash 8 Q400AT. “The Q400AT is fast, fuel efficient, and tactically flexible, operating both initial attack as well as sustained support actions from remote or urban bases. And it has strong OEM support, guaranteeing availability of parts and servicing for years,” continued Jeff. The tanker can carry 2,640 US gallons (10,000l) of retardant, foam or water and travel at 340 knots (630 km/h).

© Daniel VA Wikipedia - AT802 Air Tractor
To convert the aircraft into an airtanker, Conair outfits the frame with a proprietary Next Generation Retardant Delivery System (RDS). A team of Conair engineers designed the custom, purpose-built composite tank to deliver a 10,000-l payload of water, gel or retardant, with the ability to provide multiple coverage levels from a single drop using a computer-controlled flow system operated by pilots, ensuring the airtanker could respond to a wide variety of wildfire types, from grass to dense forest.
The tank is attached to the exterior of the aircraft under the center fuselage, enabling the interior of the cabin to remain pressurized, creating a safer environment for pilots by reducing fatigue. In a certified, multi-role version of the aircraft, the 220-inch-long tank can be removed and reinstalled in a few hours. This enables the aircraft to efficiently perform additional roles in emergency response, including cargo, passenger, medevac, or combi-transport, without compromising its aerial firefighting capability.
To enhance its superior aerial firefighting performance, the Q400AT flight deck is equipped with a Conair-developed, and Transport Canada-certified, Flight Envelope Awareness System, which provides pilots with enhanced safety awareness information such as instantaneous G-Loading, slow speed awareness, flap over-speed advisory, and angle of attack detail. Conair ‘proactively improves management systems with innovative technologies that go beyond regulatory compliance’, said the company.
The Q400MR has been in operation in France for the past 15 years while the new Q400AT just completed its first bushfire season in Australia, with its first fire season in North America scheduled for this summer.
AT802 Air Tractor/Fire Boss
When equipped with amphibious floats installed by Wipaire, the AT-802F becomes the Fire Boss scooper air tanker, able to land on and scoop water from nearby lakes, rivers and reservoirs. From a nearby water source, the 802F Fire Boss can deliver up to 14,000 gallons per hour for extended attack or ground support. An unimproved runway or water-side ramp and fuel are all it needs.
Powering the Fire Boss is the Pratt & Whitney PT6A-67F turboprop engine, which boasts 1,600 horsepower, and allows maneuverability in mountainous and / or hot operating environments.
Air Tractor’s Gen II Fire Retardant Dispersal System (FRDS) offers an extensive update to the original FRDS system, and includes more than 270 lbs of weight reduction, all-electric operation, 25-per-cent more flow rate, integrated AFF tracking / ATU telemetry system, integrated foam injection control, and, according to the company, has much simpler operation than previous systems.
In the cockpit, the FRDS Pilot Interface offers a multi-function DataVault controller with an anti-reflective, color OLED screen and backlit silicone button overlay for clarity and visibility in all lighting conditions. When approaching the fire line, pilots can dial in the coverage level, drop amount and ground speed; then, with a press of the trigger, the FRDS computer does the rest – opening and closing the fire gate doors while compensating for G-loads, gallons in the hopper, and ground speed to deliver consistent coverage along the entire drop.
AT-802F aircraft with Gen I and Gen II firegate systems can be upgraded with Gen III FRDS components. The Gen III firegate can be easily retrofitted to AT-802F airplanes equipped with Gen I and Gen II firegates. Vent doors, fairings, brackets, E-dump handle, and many other items from earlier FRDS systems can be re-used – an important aspect of commonality of parts.
DC-10
The McDonnell Douglas DC-10 is an American wide-body airliner manufactured by McDonnell Douglas, intended to succeed the DC-8 for long-range flights. It first flew in August 1970, and was introduced in August 1971 by American Airlines. Since 2006, DC-10 Air Tankers have been in service as aerial firefighting units. The aircraft, operated by the joint technical venture 10 Tanker Air Carrier, are converted wide body McDonnell Douglas DC-10-30 passenger jetliners.
10 Tanker Air has been operating (since 2006) as one of the only fleets in the world with newly developed VLATs (very large air tankers), four of which are currently in operation. Each one can carry a retardant payload of 9,400 gallons at an approximate weight of 84,600lbs. The tank system is able to drop a full load of retardant in four seconds, from a height of between 200 and 300 feet above ground level. Each aircraft is followed by seven technicians, who carry a range of spare parts and equipment with them.
Bill Pilcher, Director of Business Development for 10 Tanker Air Carrier, explained to AirMed&Rescue why the company chose the DC-10 as a firefighting aircraft in the first place, identifying four key attributes:
“We wanted to mount high-volume retardant tanks externally; the DC-10 fuselage is high enough above the ground to permit attachment of external tanks with 45,000-l capacity; the three jet engines provided for system redundancy and superior power-to-weight ratio, especially important for maneuverability; and the DC-10 could easily carry the additional weight.”
Technical adaptations made immediately in order to bring the aircraft up to spec as a firefighting plane include removal of all passenger seating and overhead bins, as well as the removal of the center main landing gear to make space for the tanks. A Supplemental Type Certificate was required and obtained for the tank mounting system.
Asked about how the longevity of the aircraft as firefighting assets would be assured, Pilcher said: “We will periodically review the current computer-controlled drop system, and we have also ensured that our software architecture allows for upgrades and modifications.”

BAe 146
When Neptune Aviation Services replaced its Korean War Era, former US Navy P2V Neptunes, it selected the BAe 146 jet airliner as its next-generation aerial tankers. Once operating as many as 11 P2Vs as air tankers for fire retardant dropping, Neptune retired its last ones in 2017, the year before its ninth – and, to date, final – BAe 146 was modified to assume that mission. Built between the late 1980s and early 1990s, the aircraft were available for under US$2 million each. Pre-purchase, particular attention was paid to the condition of the airframes, landing gears and engines.
On average, each tanker conversion, carried out by Neptune’s technical staff, took three months, commencing with the removal of the passenger interior, and installation of a single 3,000-US-gallon (11,356.24-l) tanking system. The tank, which includes a fault detection and monitoring system, is connected to five valves, located in the former baggage compartment area – two forward and three aft of the main landing gear bay – allowing for the controlled release of the retardant. Five openings at the bottom of the fuselage for retardant discharge were added, with each reinforced by doublers.
“The goal was to maintain the BAe 146’s standard airworthiness certification. This required all the pieces of the tank to fit through the original passenger door, since the airliner was not built as a freighter with a wide cargo door,” said Nic Lynn, Neptune’s Vice-President of Operations. “We built a mockup of the BAe 146 airframe, and manufactured the tank on that fixture. It verified that when the tank was dissembled, the individual pieces would fit through the door, to be reassembled on the aircraft.”
Neptune equipped all its BAe 146s with a light operational load monitoring system, which measures 34 parameters from accelerations to airspeed, altitude, location, and fuel and retardant quantity. Additionally, a heavy operational load monitoring system tracks the same 34 parameters, and records input from 27 strain gages and three additional accelerometers. All data generated from those sources is downloaded to a laptop primarily through Wi-Fi, but also via cable as a backup.
"The analysis ensures that we are maintaining the aircraft safely. Using the data, we are able to update our inspection program, which is done every two years,” Lynn noted.
In fact, the aircraft’s new role has necessitated special inspections. For instance, those parts of the airframe that come into contact with the retardant are inspected for corrosion. The engine ignitors, used during takeoff and approach in passenger operations, are also inspected. “With each retardant run equating to a low approach, our ignition systems operate more frequently than they did in airline usage, so we have adjusted their inspection intervals to accommodate this,” Lynn noted.
C-130
The C-130 entered service with the US in 1956, followed by Australia and many other nations. During its years of service, the Hercules family has participated in numerous military, civilian and humanitarian aid operations. The C-130 Hercules is the longest continuously produced military aircraft at over 60 years, with the updated Lockheed Martin C-130J Super Hercules still being produced now. It can be adapted for use as an aerial firefighting asset through the addition of a firefighting retardant delivery system.
Maffs Corp. is a combination of two aftermarket support companies, United Aeronautical and Blue Aerospace, and produces the MAFFS (Modular Airborne Fire Fighting System), which can be added to a C-130 Hercules. Final US Forest Service certification for this model was achieved in 2010, and eight systems are currently in use by the US National Guard. With a 3,000-gallon capacity, the MAFFS was initially the only roll-on / roll-off retardant delivery system available.
Coulson Aviation has since introduced its own Coulson RADS-XXL 4,000-US-gallon roll-on roll-off tanking system, which is currently utilized in all seven USAF Hercules C-130 aircraft operated by the Department of Forestry and Fire Protection in California (CAL FIRE).
RADS-XXL has a flow rate of 1,600 gallons per second, carrying up to 4,000 gallons more retardant.

© K R Weiss - Chinook CH-47
Chinook CH-47
Originally designed by Vertol in 1957, the Chinook has been through many iterations; one of the most substantial variants to be produced was the CH-47D, which first entered service in 1982; improvements from the CH-47C standard included upgraded engines, composite rotor blades, a redesigned cockpit to reduce workload, improved and redundant electrical systems and avionics, and the adoption of an advanced flight control system. It remains one of the few aircraft to be developed during the early 1960s that has remained in both production and frontline service for over 50 years.
The summer of 2019 saw the introduction of the CH-47 helitankers in a joint venture from Coulson Aviation and Unical. The adaptation of the CH-47 to a firefighting aircraft was achieved through the introduction of Coulson’s RADS, and it is known as the CU-47. It features a retractable snorkel to enable faster tank refilling, and, with Garmin avionics and a night vision system cockpit, the accuracy with which it can drop its load is enhanced further.
Maintenance, repair and overhaul
Collins Aerospace works on many different firefighting aircraft, providing maintenance, repair and overhaul (MRO) services to keep these sometimes-aging workhorses in the air. These include Canadair CL215 and CL415 purpose-built waterbombers, C-130, Sikorsky S-70 Firehawk, Bell Huey/205, Bell 212/412 family, and the Leonardo AW139.
Together with Viking Air Limited, the OEM for the CL215 and CL415, Collins is redesigning and updating these older airframes with modern avionics. At the heart of the CL-415EAF (Enhanced Aerial Firefighter) modifications is Collins’ Pro Line FusionTM flight deck. Combined with new angle of attack sensors and numerous aircraft improvements, it is designed to add greater mission effectiveness to this already proven platform.
Company spokesperson Al Killefer spoke to AirMed&Resue about the company’s latest innovations, which aren’t only on the aircraft, but also for the pilots who fly them: “Collins’ Head Up Display (HUD) system offers game-changing technology for aerial firefighting.
The HUD’s synthetic Enhanced Vision System (EVS) allows pilots to ‘see’ through smoke, fog, dust, haze and precipitation – significantly expanding capabilities by removing many current barriers to operations. Collins is currently in discussion with the US Air Force about installing its new digital HUD with enhanced vision on Air National Guard C-130Js equipped for aerial firefighting, giving hope to the idea of 24-hour aerial firefighting capabilities.”
In addition, the company has also upgraded Air National Guard C-130Hs equipped for aerial firefighting with its NP2000 propeller system. By providing a significant thrust increase at low acceleration compared to the C-130H’s legacy equipment, NP2000 helps boost operational efficiency and performance for C-130Hs flying at low speeds, close to the ground with heavy payloads to complete their firefighting missions.
Firefighting aircraft are frequently multi-mission aircraft, and investment in an airframe can also come in the form of adding a hoist capability that will allow the helicopter to become a SAR platform if needed. When it comes to aerial firefighting, key issues for hoists include:
- Weight – a lighter hoist means more weight available for water
- Ease of use – high-pressure missions require intuitive operation
- Ease of maintenance – designing hoists that are easily repaired to stay mission ready
“Over time,” Killefer said, “we’ve seen the evolution from a Huey with a removable internal hoist (installed as and when needed) and external Bambi bucket on the cargo hook, to a dedicated, multi-mission helicopter with permanent water tanks and hoists, immediately ready for whatever mission is needed. With aircraft growth has come extra power available to hoisting, so now the Firehawk, for example, has a high-speed AC hoist that enables faster hoisting than those used on the smaller Bell 412 and AW139.”
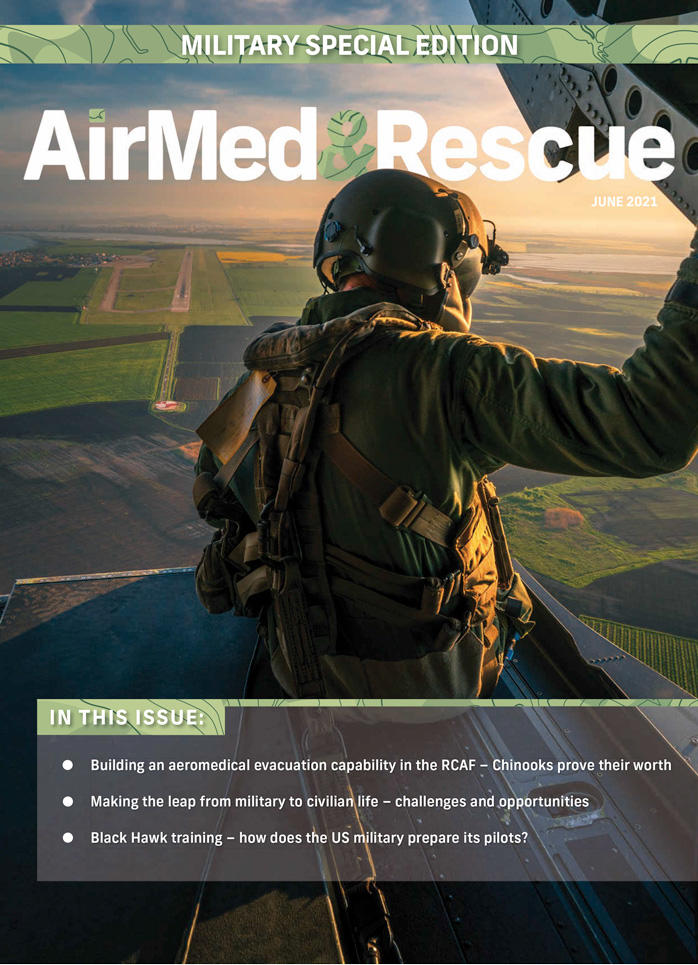
June 2021
Issue
In this issue:
- Building an aeromedical evacuation capability in the RCAF – Chinooks prove their worth
- Making the leap from military to civilian life – challenges and opportunities
- Black Hawk training – how does the US military prepares its pilots?
- Giving old aircraft a new lease of life as aerial firefighters
- Interviews: US Air Force PJs past and present; Dr Neville Vlok, HALO Aviation
- Provider Profile: Keewatin Air
Mandy Langfield
Mandy Langfield is Director of Publishing for Voyageur Publishing & Events. She was Editor of AirMed&Rescue from December 2017 until April 2021. Her favourite helicopter is the Chinook, having grown up near an RAF training ground!