Company Profile: Kopter
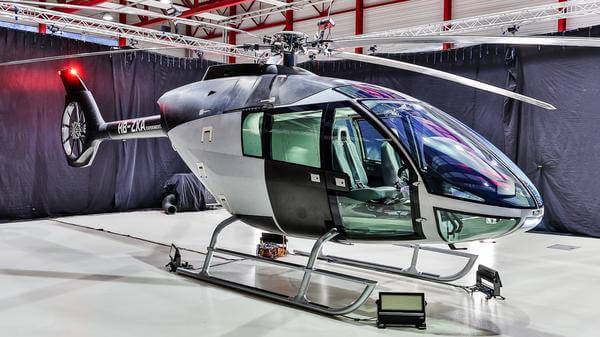
Entering the headquarters of Kopter in Wetzikon, Switzerland, what immediately strikes you is the air of quiet excitement; as well as the large helicopter placed in the middle of the open plan office – the first prototype of the SH09 has been given pride of place in the building
The team at Kopter is right now working steadily towards its goal of certification of its SH09 helicopter, which will happen during the second half of 2019, with P3 (the third prototype) to head into flight testing in the coming weeks.
For CEO Andreas Löwenstein, the ramp up towards delivery of the helicopters to the first customers is an exciting time, and one he has been working towards since he joined the company some 18 months ago. With more than 28 years of experience in the aerospace and defence industry, having worked at EADS and Eurocopter in the past, there is little doubting the fact that he knows what the market needs, and for him, the opportunity to be at the helm of a company that is delivering a brand-new helicopter to the market was one that he couldn’t pass up. “I’ve always been a builder,” he told AirMed&Rescue, “whether that is building a company or building a team. To bring together the team and knowledge that inspires the spirit of innovation is a very enjoyable experience.”
A costly one though – CHF300 million (€253,670,343) has been spent so far, and certification has still to come. In a move new to the industry, Kopter is aiming for dual accreditation from the European Aviation Safety Agency and US Federal Aviation Administration at approximately the same time – ambitious, for sure, but achievable, said Löwenstein, depending on how the two agencies will work together, which seems to be going very well today.

Fresh approach
Designed originally in 2009 by Martin Stucki from scratch, with large rear-opening cargo doors and no separation between the cockpit and the cabin, the spacious interior of the SH09 allows for a wide range of configurations – emergency medical transport, surveillance and law enforcement, utility, and passenger transport. Its modular design means that the change from one mission profile to another can be effected quickly and easily – from adding another stretcher, to moving the pedals from the second pilot’s seat in order to allow an additional passenger to sit safely in that seat without risking an accidental movement of the pedals by that passenger. Löwenstein used the term ‘a flying Swiss Pocket knife’.
Löwenstein has mentioned in the past that innovation in the helicopter market is notable by its absence – ‘it’s easier for manufacturers to stick with what has been tried and proven’, he said.
So, what is different about the SH09 to other aircraft? “New technology has allowed for a change in fundamentals – the helicopter architecture being one,”
New technology has allowed for a change in fundamentals – the helicopter architecture being one,
he said. “Being made from composite materials means it is both light and crash resistant. The second revolution is the additional safety features that we have put on the aircraft as part of the initial design – these (such as many dual systems) are often optional extras [on other aircraft]. Finally, the cost of maintenance and operation will be lower.” There was mention too of linking the digital systems of the aircraft and some more sensors with an app on the customer’s mobile device, which would allow connected services, enabling for more efficient maintenance processes.
The cabin of the SH09 will come equipped with a full glass cockpit, with an avionics suite from Garmin – the newly launched G3000H. “The G3000H will ease the workload of SH09 pilots while providing best-in-class situational awareness. This will enable a higher level of safety for every mission, the core principle behind the design of our helicopter,” noted Michele Riccobono, Kopter Executive Vice-President Technology. Safety has been at the heart of the helicopter’s development from its inception.
The air medical industry will without doubt be a key customer segment for Kopter – for the past 18 months, it has been working on the interior cabin design with Metro Aviation, one of the largest providers of air medical services in the US. This has resulted in more space for stretchers, better access to the patient (s) for the medics, and more space made available for medical kit thanks to the movement of a fuel tank from the cabin wall into the cabin floor.
Kopter’s manufacturing and flight testing departments are in the dramatic landscape of a valley near Mollis, not far from its headquarters in Wetzikon, and although currently it only has the one hangar, plans are afoot to build a 16,000m2 facility in 2019. Production of certain parts of the SH09 – such as the five rotor blades – are done in-house. Most, though, are sourced from third party suppliers. While every effort has been made to ensure the finest quality for each of the thousands of components from which a helicopter is built, there are almost inevitably some teething problems. One such issue has been with the dynamic components provided by a supplier in the third prototype (PS03), which will (once fixed!) be off to Sicily for three quarters of intense testing, where it will be put through its paces and pushed to – and past – its operational limits. The small delay in getting the P3 to Sicily for testing has actually had a beneficial side too – the company is taking advantage of the schedule shift to refine a number of subsystems where areas of further optimisation were identified during ground testing. While these refinements were meant to be phased into the PS4 (Pre-Series 4) aircraft, by putting them onto the P3, the development programme can be accelerated. The PS4 will be the aircraft submitted for certification, which Kopter expects will be achieved next year, ensuring the first aircraft can be delivered to customers before the end of 2019.
The SH09 has been built in the knowledge that parts can be made here, and tested here, but can ultimately be put together in other countries
While currently the plan is to build the helicopters in the facility in Switzerland, there will be a time in the near future, according to Löwenstein, when this will not be the case: “The SH09 has been built in the knowledge that parts can be made here, and tested here, but can ultimately be put together in other countries."
There will be a manufacturing facility in the US before long, he said, and there are also plans to expand to the Asia Pacific region. Assembly facilities around the world are a sensible move – not only to ensure compliance with local laws and regulations, but lso because it is a much more cost effective way of doing business, he explained, as Kopter will be able to meet local operator requirements for customisation of the helicopter.

Market opportunity
The belief in the product among the Kopter employees to whom AirMed&Rescue spoke for this article was infectious. Christian Gras, Executive Vice President of Customers, has lengthy experience in the industry, and is passionate in his belief that strong, adaptable single-engine helicopters such as the SH09 are the future of the industry. “Kopter,” he said, “is going to shake up the hierarchy of the helicopter manufacturing sector.” Having worked in the US, Europe and South America, Gras’s understanding of market dynamics is impressive. Identifying gaps in the market and being able to exploit them is key to success in any business, but in the relatively dense aircraft manufacturing business, it is more important than ever.
The growth of the helicopter emergency medical services sector in the US will continue, he says, and through a close strategic co-operation with Metro Aviation, Kopter is planning on holding a strong position in this area in years to come: “We are going to aim to take a significant per cent of the market in the next 10 years,” he told AirMed&Rescue. With many operators in the US still using the AS350 Ecureuil, the time will soon be nigh for these helicopters to be put out to pasture, and thus comes the opportunity for the SH09 to potentially become the aircraft of choice. While it is possible that other manufacturers could downgrade a twin-engine aircraft into a single-engine one, question marks hang over whether or not this would be a profitable move for them.
Kopter’s first customers of the SH09 ‘will be partners’, said Jan Nowacki, Executive Vice-President of Operations. Kopter isn’t going to deliver hundreds of helicopters in the first few years. There will be time for feedback from these initial customers, with the opportunity to improve and streamline processes and services. Without data from these customers, the company is unable to progress further. “It is normal in a complex technical development process that unforeseen circumstances will appear,” said Löwenstein, “and we have mitigation processes in place for when that happens.”
A passion for what they are doing is apparent throughout the layers of the company, from the CEO to the Chief Safety Officer, who explained in detail the inner workings of the helicopter prototypes and the testing that was going to be taking place. Kopter is not innovating for the sake of it – the team has the experience to know what can be improved upon, and is taking the opportunity to do just that, with new technology allowing for the introduction of an aircraft that offers real mission versatility and enhanced safety features.
The EMS helicopter of the future? Maybe.
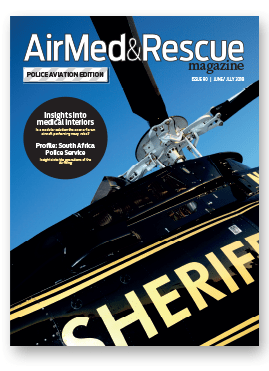
June 2018
Issue
Mandy Langfield
Mandy Langfield is Director of Publishing for Voyageur Publishing & Events. She was Editor of AirMed&Rescue from December 2017 until April 2021. Her favourite helicopter is the Chinook, having grown up near an RAF training ground!