Certified action: approving the equipment in and around the aircraft
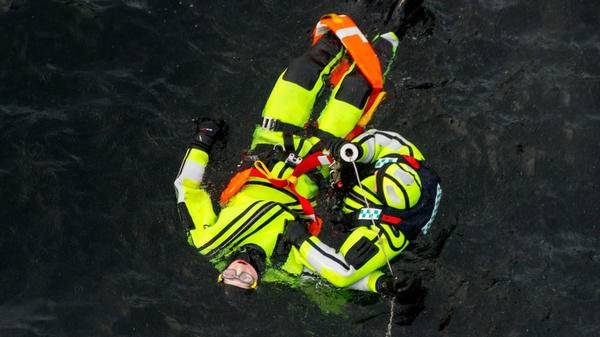
Khai Trung Le speaks to helicopter equipment providers CleanSpace, Lifesaving Systems, ISOVAC, Lite Flite, Northwall, and Renew Biomedical on the complexity and criticality of certifying equipment for use in and around the aircraft
This isn’t an article about Covid. But its long shadow is inescapable, and the 2020-21 pandemic shone an undeniable light on the tangible benefits of certification and approval. Nicola Campani, Chairperson and Founder of Northwall, was forthright about the threat when equipment fails to meet standards: “European civilian emergency services didn’t experience the Ebola crisis directly, and any containment efforts from European providers came from military services.
“During the first Covid wave, the European market was flooded by generic isolation devices with not enough safety or efficacy and did not consider patient isolation as a decisive measure within the hospital system. As a result, in Italy specifically, the state had many doubts about even classifying isolation units as medical devices within its pandemic response procurement.”
Covid elevated both the need for specialist equipment and awareness of the need for quality certification and approval. AirMed&Rescue frequently discusses aircraft certification, but just as integral is ensuring the equipment used within and around the helicopter is fit for purpose and can maintain safe handling and functionality in rigorous and demanding scenarios.
Demand satisfaction
Certifying equipment for aircraft use can be lengthy and demanding. Jorge Marchan, Operations Manager at ISOVAC Products, stated that ‘the certification process […] is extremely elaborate and requires years of testing and documentation prior to marketing approval’.
Bella Nyugen, Global PR Manager of CleanSpace Respirators, noted that aviation regulations also require a piece of equipment to be certified as compliant for each particular aircraft type. In particular, she commented: “Factors normally considered for equipment on aircraft, in addition to the safety and wellbeing of the patient include flammability; restraint of objects of mass in the cabin, accessibility to emergency exits; trip hazards; head strike issues; and battery or power supply (EMI, fire, power and charging requirements).”
Certification and approval must address split priorities. On one hand ensuring quality standards meticulously defined within a large regulatory body and communicated and enforced across multiple industries and sometimes multiple countries, but also matching the pace of adoption of new materials and disruptive technologies. Mario Vittone, General Manager of Lifesaving Systems, commented on the development of certification on helicopter hook hoists: “In the past decade, the certification process itself has improved for Human External Cargo equipment, owning mostly to increased availability of the US Federal Aviation Administration (FAA) to assist manufacturers with these efforts.
“As more and more operations employ hoist short-hauling in their rescue efforts with helicopters, I think the regulators will continue to work with industry to ensure the products are safe and effective. Expanding the standards for gear approval – adding TSOs for rescue baskets, litters, and other equipment – is the challenge for the next decade.”
Ultimately, as Lite Flite CEO Thomas Knudstrup detailed, the certification process remains as knowable as ever: “When it comes to certification law, the European Regulative 2016/425 and associated European Standards such as EN813 and EN358 have remained approximately the same. It includes use of a national accredited notified body that will perform the testing, reporting, and finally issuing of the certificate.” As these standards become recognized, it becomes the responsibility of the operator to gaining approval to fly with these products, although there are exceptions. Knudstrup continued: “One major aircraft manufacturer has chosen Lite Flite equipment in their certification of SAR-configured helicopters.”
The military addition
One may expect certification and approval for military use to be more strenuous and demanding than in civilian environments, and equipment providers are frequently explicit with publicizing whether devices have been approved for military use. However, Vittone noted that the differences can be smaller than expected: “The difference can be dramatic in terms of speed of the authorizations, but the testing requirements are generally identical. Before authorizing the 414 D-LOK, we had to provide icing, salt fog and dust, fatigue, as well as drop shock, ultimate breaking and gate strength testing.”
Marchan also confirmed that, for ISOVAC, there was little distinction between military and civilian sector use in the certification process, noting that both require US Food and Drug Administration (FDA) clearance when transporting a patient using a patient isolation unit. He further stated: “Testing under US military standards has not particularly changed much over the years, but material advancements have allowed ISOVAC to diversify its products to better meet mission-specific requirements during chemical, biological, radiological, and nuclear events.
“Over the years, ISOVAC has been fortunate enough to work alongside the US Department of Defence (DOD) during the design phase of our projects, which allowed testing to be conducted under the most rigorous conditions and held to the highest standards. In turn, we were able to provide the civilian market the justifications needed for FAA requirements while also meeting the needs of the DOD.”
However, according to Campani, the situation differs outside of the US: “In Europe, military systems have their own certification and approval process and dedicated authorities. They don’t require the same features and test procedures as civilian authorities, and civilian SAR/HEMS requires more detailed documentation to reach approval.”
Despite the greater documentation required in many civilian certification processes, Knudstrup also noted that, while Lite Flite hoist harnesses have received numerous European certifications, ‘there are no European Technical Standard Orders (ETSO) covering that kind of equipment. This means that, for example, should an Australian operator ask for Civil Aviation Safety Authority -approved equipment, we cannot simply refer to an EASA ETSO and have the equipment approved on the usual bi-lateral agreements’.

Iterative steps
The certification process’ lengthiness can be shortened if gaining approval for an iterative product, and Marchan noted that ‘it all comes down to how significant that modification is to the safe use of the device’.
Campani stated: “There is reciprocity between US and European Union test validation, but not in the final approval and classification of devices, as we’ve experienced with the ISOVAC Capsuls being Class II for the US FDA. Different is the condition of tests and approval between aeronautical authorities, wherein reciprocity is much higher.”
Within authorities in the US, Vittone said: “Both FAA and CASA have very similar processes for approving minor design changes to equipment that holds an approval. It’s not that the process is necessarily transferable, but it can be much easier if that equipment is made from similar processes or parts of a previously approved item. Lifesaving Systems has tested every type of attaching and adjusting hardware we manufacture for use on harnesses, for example. We won’t have to recertify that hardware, should we make a new harness configuration. That saves time and money, of course; the second certification was, for us, half the effort of the first.”
Howevery, Knudstrup spoke enthusiastically about the multiple advantages of certifying iterative products: “It is a huge advantage that previously performed tests can be re-used, as most of the materials and parts remain the same; with a bit of planning, new Lite Flite products based on previous products can be certified within six-eight weeks. However, if the difference is yet smaller, new products are often simply added within the same certification, due to more flexible civilian certification over traditional aviation certification through EASA, CASA, or the FAA, for example.”
Taking the thorough route
Certification can take long and expensive years. But when asked about whether the process would benefit from expediency – and AirMed&Rescue acknowledges the coarseness of our query – Vittone was unabashed about the risk this may result in. He stated: “This is aviation. People hanging on to a helicopter for their lives. Expediency always sounds like rushing to me; I think it is important for the process to be comprehensive. It’s when comprehensive morphs into redundancy of effort that I think changes can be made.”
Marchan was similarly effusive about maintaining the meticulousness of certification, noting: “By eliminating or expediating certain processes, you potentially risk the safety of the general public. Take our current pandemic and the market flood of patient isolation systems, for example. None of which were fully certified and led to a multitude of patient safety incidents in numerous markets around the world. ISOVAC takes pride in the full process of certifications as it helps make our products what they are today.”
However, Northwall – which is supporting ISOVAC in getting its isolation units certified in Europe – detailed how certification outside of the US can struggle with a lack of clarity in classifications. Campani said: “Redundancy in certification processes in Europe is high because the classification of containment devices is not clear, hence the need for numerous tests, sometimes in conflicting and incompatible directions.
“The certification systems and methods are constantly changing in a push for harmonization between local and European authorities specializing in medical devices and airworthiness, and often the certification requirements are not adequate or in step with current technological and technical developments. The push from manufacturers in the standardization committees is fundamental to keeping pace with testing, quality of materials, and the ability of new technologies to maintain safety and effectiveness of performance.”
Knudstrup noted that while ‘expediency or rushing will only lead to problematic or questionable certification’, the process might benefit from a more flexible definition of fit, form, and function terminology, as well as greater acceptance of civilian organization approvals, a step entities like EASA are already taking.

New from the old
Airborne special missions communities have long looked to pre-loved helicopters as a cost-saving measure. For example, former military helicopters have long furnished law enforcement agencies. But, as Mark Taylor, President and Owner of Renew Biomedical, states, this has not always been the case for devices within the helicopter: “In the past, aeromedical transport companies were limited to the types of equipment that could be taken onboard due to environmental and safety issues.”
Renew Biomedical, and sister company Master Medical Equipment, refurbish securing and mounting medical equipment for both fixed- and rotor-wing aircraft, which can bring not only bespoke certification challenges, but also preconceptions of its userbase. Taylor stated: “Our challenges are to make sure all equipment has the correct original parts, new accessories, and are cosmetically appealing to our customers. While they are not the same as new products, technical and operational performance must exceed OEM specifications, as well as our own ISO 13485:2019 quality specifications.”
This necessitates meeting FAA and other crash ratings and environmental factors for altitude and temperature, and often means having to exceed OEM standards.
The root need
If the pandemic was a rude awakening in the essentiality of certification and approval, what next for the future, and the undeniable reality of future threats to global healthcare? Campani commented: “Future pandemic events must be approached through enabling all standard resources to answer any emergency, insulating a contaminated patient and protecting the rest of aircraft crew and recipient hospital, and allow immunodeficient patients to continue to use hospital services safely.”
Nyugen also said: “Throughout the pandemic, emergency patient retrievals continue apace. Our frontline healthcare customers frequently remind us that you cannot design the close interaction with patients in distress out of their jobs. Being up close and personal is a patient care necessity in these circumstances.”
This is being reflected in purchasing attitudes. According to Marchan, end-users are shifting from a ‘buy-anything’ mentality to have a more familiar understanding of regulatory requirements. “We definitely see the market realizing that they were unprepared for what happened at the beginning of 2020 […] The likes of the FDA, FAA, European Aviation Safety Agency (EASA), and even Customs & Borders have enforced their authority, and fully certified systems are now taking priority in the regulatory process.”
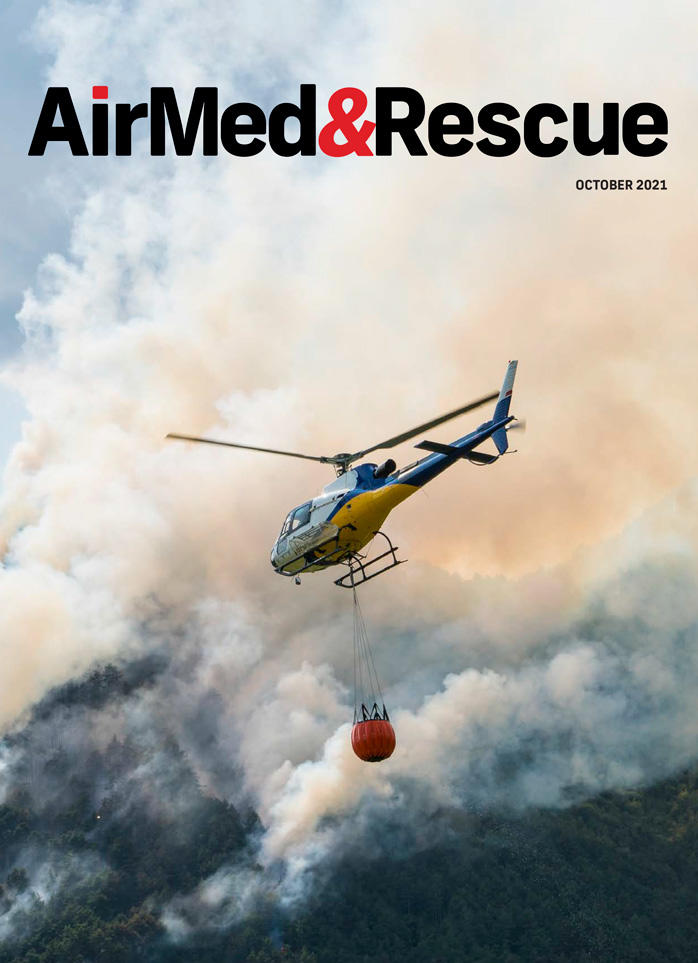
September 2021
Issue
Keeping our aerial firefighters safe
As the volume and risk of missions increases, what can we do to make aerial firefighting aircraft and crew safer?
Certified action
Cleanspace, Lifesaving Systems, ISOVAC, Lite Flite, Northwall, and Renew Biomedical discuss the criticality of certifying equipment in and around the aircraft.
Kyle Madigan, BCEN
Madigan outlines the extensive history of the BCEN and its evolution to serve the needs of certified nurses
Khai Trung Le
Khai Trung Le is Editor of AirMed&Rescue. He is an experienced science writer, having previously been embedded in Cardiff University College of Physical Sciences, Innovate UK research council, and the UK Institute of Material Sciences. His writing can also be found on Star Trek and Vice.