Aviation industry addresses climate concerns
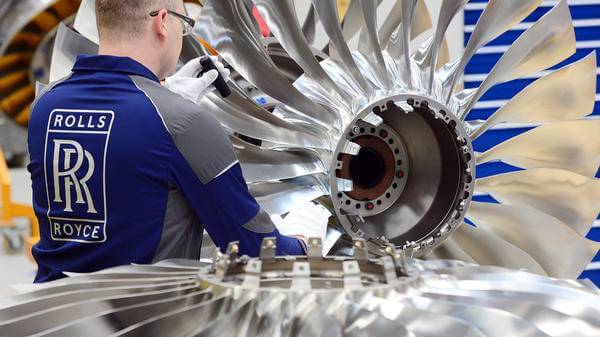
James Paul Wallis looks at the latest efforts by the aviation sector to minimise the effects of emissions from the global air rescue and air medical industry
“Climate change is one of the defining challenges of our time.” No, not the words of Greta Thunberg or an environmental scientist, but of Jason McLean, CEO of McLean Group, who was speaking in October 2019 when the Group’s subsidiary Blackcomb Aviation announced it had become carbon neutral. An eye-catching move for an organisation working in the aviation sphere, given that transport as a whole is not the greenest of sectors, and aviation is often singled out as being particularly non-eco-friendly.
The key problem is that current aircraft burn large quantities of fuel and produce carbon dioxide in the process. John Morris, Blackcomb Aviation General Manager and Director, noted: “For now, we’re stuck with jet-fuel-powered turbine engines. In my 40 years in the industry, burning jet fuel has been a constant and there are really no near-term alternatives to gas turbines for the missions expected of us.”
So, how do you save lives while also saving the planet? Well, one way to mitigate the environmental effects is to offset your carbon footprint by contributing to environmental projects. That’s been the approach of Blackcomb Aviation, which announced it had gone carbon neutral. The Canadian operator, whose helicopters are employed in roles from tourism to SAR support, medevac and wildfire suppression, has achieved this through ‘the sequestration of greenhouse gases by preserving forests, encouraging greener travel for commuters, and incorporating energy savings and lower emissions in new building design’.
That’s one route. But what can be done to make the aircraft themselves greener?

Pratt &Whitney
Fuel efficiency
Over the decades, internal combustion engine design has improved to develop more power from less fuel. Looking at business aviation specifically, Louise Solomita of Bombardier noted that fuel efficiency has improved by 40 per cent over the last 40 years. And the improvements keep coming – Pratt & Whitney’s latest GTF geared-fan engines burn 16-per-cent less fuel and reduce nitrogen oxide emissions by 50 per cent compared to the regulatory standard, says the company.
Meanwhile, Safran’s LEAP (Leading Edge Aviation Propulsion) aims to address needs of aircraft manufacturers and their buyers. “Propulsion,” said Safran, “is now the main economic instrument for reducing consumption. LEAP provides the aviation industry with a more economical as well as environmentally friendly solution.” LEAP progress includes new fan blade technology that reduces the weight of the engine while increasing the durability of the blading. The high-pressure (HP) body, developed and manufactured by GE as part of the ‘e-core’ programme, consists of a 10-stage high-pressure compressor, with a very high compression ratio, driven by a two-stage high-pressure turbine.
Phil Curnock, Chief Engineer of Rolls Royce’s civil future programme, said at the recent Dubai Air Show that engines currently in production are ‘50-per-cent more efficient than they were 30 years ago’. That doesn’t mean more progress can’t be made though – the firm’s newest development, the UltraFan, looks to be set for commercial use in the next 10 years. He added: “And once you’ve got the latest gas turbine on your aircraft, the next thing to do is look at the fuel you are burning.” (more on that later)
A simple step, then, for operators, is to opt for the latest power units. Cecile Vion-Lancuit, Head of Communications and Marketing at Kopter, said the helicopter manufacturer uses the Honeywell HTS 900, which is known to be fuel efficient, meaning that it consumes less fuel and therefore produces less exhaust fumes.

Rolls Royce Ultra Fan
Tom Parsons, Air BP’s Commercial Development Manager, Low Carbon, gives the low down on Sustainable Aviation Fuel.
SAF is produced from sustainable, renewable feedstocks and is very similar in its chemistry to fossil jet fuel. Some typical feedstocks used are cooking oil and other non-palm waste oils from animals or plants; solid waste from homes and businesses, such as packaging, paper, textiles, and food scraps that would otherwise go to landfill or incineration. Other potential sources include forestry waste, such as waste wood, and energy crops, including fast growing plants and algae.
SAF can be blended at up to 50 per cent with fossil jet fuel and all quality tests are completed as per a regular jet fuel. Once blended, SAF has the same characteristics as fossil jet fuel. The blend is then re-certified as Jet A or Jet A-1. It can be handled in exactly the same way as a regular jet fuel, so no changes are required in the fueling infrastructure or for an aircraft wanting to use SAF.
Air BP has announced collaborations with two companies: in 2018 the company signed an agreement with leading renewable fuel producer Neste, which produces sustainable available fuel made from non-palm oil based used cooking oil and other wastes and residues. Through this collaboration, we are developing new SAF supply chains. To date, Air BP has supplied SAF at 15 locations in five countries across three continents.
SAF will play a really important role in meeting the aviation industry’s carbon reduction targets, however, we need to use all the options to reduce carbon that we have available. There are several broad opportunities for carbon reduction across the industry such as more efficient aircraft design, smarter operations and the development of future technologies like electrification.

Another part of the efficiency equation, noted Solomita, is to improve the aircraft’s design. As an example, she said: “Bombardier’s Challenger 350 aircraft is one of the most efficient business aircraft in the world. Its re-designed, canted winglets cut down on drag, reducing fuel burn.” Furthermore, using advanced composite materials can reduce the weight of the aircraft, added Solomita, which will also translate to fuel savings.
Combining these measures can have a significant impact. “Thanks to redesigned wings and brand-new, purpose-built Rolls-Royce Pearl engines, [Bombardier’s] Global 5500 and 6500 aircraft (flown by, among others, German air ambulance specialist FAI) are up to 13-per-cent more efficient than their predecessors, the Global 5000 and Global 6000 aircraft,” noted Solomita.
Sustainable aviation fuel
The problem with burning standard fuels is that you are, in effect, releasing carbon into the atmosphere that would otherwise have stayed locked up deep underground. What about a replacement liquid fuel from a sustainable source, such as vegetable oils? By burning such a fuel, you would only rerelease carbon that the plants absorbed from the air as they grew. You create a cycle, with no net increase of carbon in the atmosphere.
Such fuels have already been developed. Bombardier, for one, is advocating for widespread use of sustainable aviation fuel (SAF), said Solomita. The goal, she said, is: “[To] enable drop-in jet fuel production from multiple feedstocks and conversion processes so no changes are required in aircraft or engine fuel systems, distribution infrastructure or storage facilities. As such, SAF can be mixed interchangeably with existing jet fuel.”
Renewable sources include cooking oil, plant oils, solid municipal waste, waste gases, sugars, purpose-grown biomass, and agricultural residues. “These are inherently a cleaner choice: many naturally contribute to reducing emissions throughout their lifecycle. And by diverting these elements from landfill for fuel production, we avoid emissions associated with the landfill process,” said Solomita. “Relative to fossil fuels, which are CO2-intensive to produce, as well as to burn, sustainably produced, unconventional jet fuel results in a net reduction in CO2 emissions across its life cycle. Even when considering the emissions produced in growing, transporting, harvesting, processing, and refining a particular feedstock used in SAF production, SAF has been shown to provide significant reductions in overall CO2 lifecycle emissions when compared to fossil fuels.”
To put some figures on this, energy producer BP says SAF can offer a reduction in CO2 emissions of up to 80 per cent over the lifecycle of the fuel compared to fossil jet fuel. And BP also states that SAF is safe to use: “SAF can be blended at up to 50 per cent with fossil jet fuel and all quality tests are completed as per a regular jet fuel. Once blended, SAF has the same characteristics as fossil jet fuel. The blend is then re-certified as Jet A or Jet A-1. It can be handled in exactly the same way as a regular jet fuel, so no changes are required in the fuelling infrastructure or for an aircraft wanting to use SAF.”

Robinson's electric R44
While not yet the norm, SAF use could become widespread. The International Civil Aviation Organization (ICAO) is calling for SAF to make up a significant proportion of fuel used by 2050. And SAF is already commercially available, with production increasing from an average of just 290,000 litres per year in 2013 to 2015, to 6.45 million litres per year in 2016 to 2019, according to ICAO. The Organization claims that by 2032, SAF production capacity could be eight billion litres per year.
The price at the pump is currently higher for SAF than for standard jet fuel
Unsurprisingly, there is a catch: the cost.
The price at the pump is currently higher for SAF than for standard jet fuel. However, that situation could be reversed if, as BP says, higher demand for SAF leads to more production and thereby lower costs, or if the cost of traditional jet fuel increases.
Noise pollution
Climate change aside, there’s also the question of how to reduce noise pollution. The aim here is not to save the physical environment, but to increase passenger comfort and also, potentially, enable aircraft to operate in areas where they might otherwise be unwelcome, such as hospitals surrounded by residential districts.
Vion-Lancuit of Kopter said that one of the main achievements with the SH09 helicopter’s design has been noise reduction compared to other existing platforms. She explained: “We’ve been especially working on the design of the shrouded tail rotor to significantly reduce noise emissions. Also, our main rotor head that includes five blades contributes to lower noise levels.” Flight tests with a prototype in Pozzallo, Sicily, showed noise levels in the range of around three decibels lower than competitors under certification conditions, said Vion-Lancuit.
Pratt & Whitney also says it is investing resources into reducing the noise produced by its engines. As an example, the firm claims a noise footprint reduction of up to 75 per cent for passenger planes fitted with its GTF engines compared to conventional engines.

Pratt &Whitney
Going electric
An alternative route would be to do away with combustion altogether and develop aircraft powered by batteries, eliminating emissions and engine noise at a stroke.
Modern technology allows for batteries that can store more energy per unit mass, and this greater ‘energy density’ affords cars like those offered by Tesla high power coupled with a decent range. The key to making electric aircraft is to have a high enough energy density that the power needed to complete a mission can be contained in a battery that’s light enough to allow the aircraft to take off. If that can be cracked, then operators will be able to adopt aircraft that produce no emissions at all.
Modern technology allows for batteries that can store more energy per unit mass, and this greater ‘energy density’ affords cars like those offered by Tesla high power coupled with a decent range
One proponent of electric aircraft is businesswoman Martine Rothblatt, who has made the headlines for her project working with Tier 1 Engineering to convert an R44 helicopter to battery power. The Robinson R44 was chosen in part for its light frame with a relatively heavy engine. Although the electric motors weigh just 100 pounds, much less than the 500-pound piston power plant they replaced, the battery array (mounted on the landing gear under the helicopter’s belly) comes in at some 1,100 pounds. The work involved connecting the motors to the original drive train via a reduction gearbox, with no other changes to the drive train or the flight controls. The modified, proof-of-concept machine has been successfully flown, gaining a Guinness World Record in December 2018 for the farthest distance travelled by an electric helicopter (30 nautical miles).
Rothblatt’s interest comes from Lung Biotechnology, a subsidiary of her organisation United Therapeutics, which uses helicopters to fly remanufactured donor lungs to surgeons. She explained: “I believe electric helicopters are beneficial for medical flight for three reasons. First, they will be less expensive, with many fewer moving parts and hence much lower maintenance costs. Second, they will be quieter, enabling operation in and around a greater diversity of medical facilities. Third, they will have a lower carbon footprint. This is a competitive advantage as a rapidly increasing number of government entities are binding themselves to dramatically reducing the carbon footprints of their own operations and of those with whom they contract over the next couple of decades.”
Many other companies are also working on e-flight, from small start-ups with big ideas to mainstream manufacturers. Solutions range from new multicopter designs to diesel-electric hybrid powerplants for retrofitting into existing fixed-wing models (see for example Ampaire). United Technologies (UTC), parent of Pratt & Whitney, Collins Aerospace and more, has its Project 804, for example, a hybrid-electric X-Plane, which combines traditional engines with linked electric motors. The engines are active throughout a flight, with the motors providing extra propulsion when needed, for example during take-off. UTC is aiming for a first flight by 2022.
In December 2019, Rolls-Royce unveiled its all-electric plane, which it hopes will claim the title of ‘world’s fastest’ when it launches
In December 2019, Rolls-Royce unveiled its all-electric plane, which it hopes will claim the title of ‘world’s fastest’ when it launches. The aircraft is part of a Rolls-Royce initiative called ACCEL – short for ‘Accelerating the Electrification of Flight’ and is a key part of Rolls-Royce’s strategy to champion electrification. The project involves a host of partners including electric motor and controller manufacturer YASA and the aviation start-up Electroflight. Half of the project’s funding is provided by the Aerospace Technology Institute (ATI), in partnership with the Department for Business, Energy & Industrial Strategy and Innovate UK.
As another example, Airbus officially opened its new E-Aircraft System House in October. The facility will serve as a test centre for alternative energy sources and propulsion systems. Airbus has said it aims to produce the first generation of zero-emission commercial aircraft sometime around the 2030s, and with an investment of €50 million, it seems they’re serious.
As for cost, unlike SAF, electricity could work out to be much, much cheaper than conventional fuels. For example, Roei Ganzarski, CEO of magniX, which is working on electric motors for the aviation industry, is on record saying that while a 100-mile flight on a conventionally powered Cessna Caravan might use $400 of fuel, an electric version could complete the same flight for around $10.

Manufacturing and materials
Another way to improve eco credentials is for manufacturers to reduce the carbon footprint in the factory. An example would be the increasing use of 3D printing of components, which Solomita of Bombardier noted reduces the amount of waste in the manufacturing process.
Solomita added that Bombardier also assesses environmental impact before implementing a new material or technology. This includes cabin materials. As an example, she said: “A number of Bombardier suppliers offer a veneer product called ‘true wood’ that is actually made from production cut-off waste from several veneer species including walnut and oak.” The firm also uses veneers that are certified by the Forest Stewardship Council, indicating that they have been sustainably harvested.
Helipads
Another area where operators might make changes for environmental considerations is in their facilities on the ground, including helipads. A popular construction for helipads, particularly at ground level, has been to use poured concrete, but the cement needed is particularly energy intensive to produce. An alternative is aluminium; although the energy needed to extract the metal from its ore is high, there is the advantage that aluminium can easily be recycled.
reuse trumps recycling, and FEC Heliports noted that helipads made of aluminium, such as its HELISLAT and HELOMAT designs, can be relocated as needed
Generally speaking, reuse trumps recycling, and FEC Heliports noted that helipads made of aluminium, such as its HELISLAT and HELOMAT designs, can be relocated as needed.
For short-term use, rather than pouring a concrete pad that will soon be abandoned, there are portable aluminium pads available, such as the FEC Portapad.
As in other areas, the lighting options for helipads have become more energy efficient over the years too. Mike Bishop, Sales and Marketing at FEC Heliports, explained that the company provides perimeter and obstruction lighting that can run either from the mains, or from a low-voltage supply, which is ‘ideal for solar and battery power supply’. Discussing the company’s portable HEMS-Station lighting system, he said: “The HEMS-Station can be powered from a 110-230V AC mains supply, 13.5-28V DC supply or a solar array, wind turbine or any combination of the above, automatically switching to the lowest cost/greenest source of supply.”
Green future
One way or another, it’s likely that planes and helicopters will continue to get greener all the time. If you’re still dubious on whether electric aircraft will take off (pun intended), your doubts are not shared by Norway, which announced in 2018 that by 2040 all short-haul (under 90-minute) passenger flights will be all-electric.
And it’s not all about the manufacturers. There are small steps any company can take – the mantra of ‘no change too small’ applies to everything from ditching takeaway coffee cups in the base, to carbon offsetting, as adopted by Blackcomb Aviation. As Jason McLean said when the operator reported its carbon-neutral milestone: “We can’t simply leave it to regulators to fix things for us. Businesses also need to adapt and help lead the transition to a lower carbon economy.”
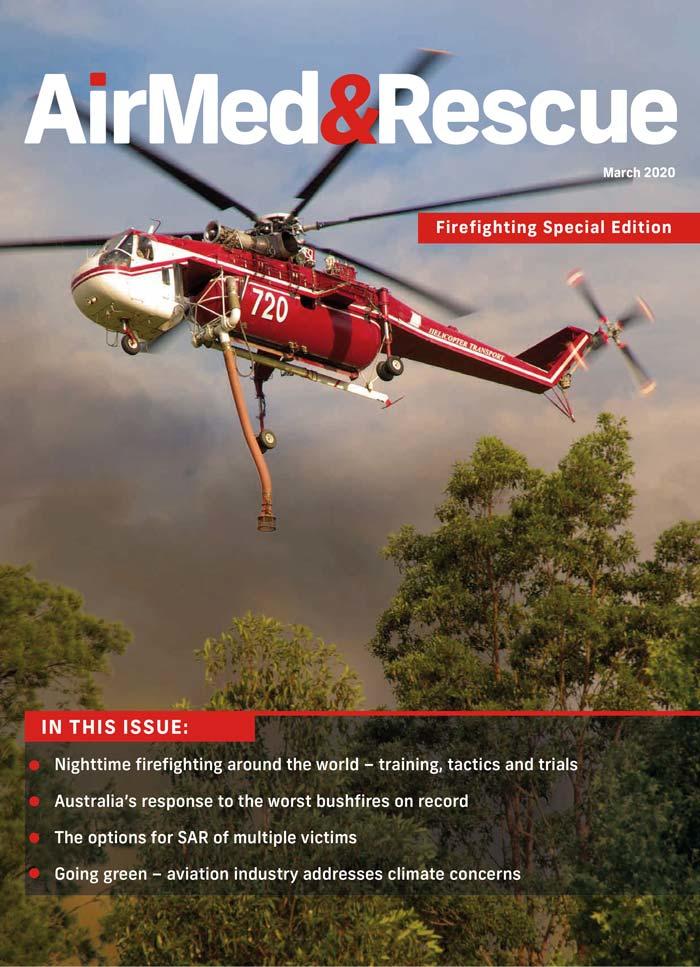
March 2020
Issue
In the Firefighting Special Edition
- Nighttime firefighting around the world - training, tactics and trials
- Australia's response to the worst bushfires on record
- The options for SAR of multiple victims
- Going green - aviation industry addresses climate concerns
James Paul Wallis
Previously editor of AirMed & Rescue Magazine from launch up till issue 87, James Paul Wallis continues to write on air medical matters. He also contributes to AMR sister publication the International Travel & Health Insurance Journal.