Air Ambulance aircraft innovation and enhancement
Technology that was once only to be found in science fiction novels is fast becoming reality, as advances in avionics, composite materials and connectivity bring enhanced services and safety to the air ambulance sector. James Paul Wallis reports
Technology that was once only to be found in science fiction novels is fast becoming reality, as advances in avionics, composite materials and connectivity bring enhanced services and safety to the air ambulance sector.
It took 450 years for the fantasy helicopter imagined, described and drawn by Leonardo da Vinci to evolve into the planet’s first practical rotor-powered flying machine. Igor Sikorsky’s VS-300 took its first untethered flight at Stratford, Connecticut in 1940, and since this time, helicopters have become vital – and ever lighter, nimbler and faster – assets not only for armed forces but also for emergency medical and rescue services. Now, though, the industry is moving faster than ever, with better engines powering lighter aircraft, while developments in avionics mean pilots can fly more safely and patients can receive better care from medics using enhanced kit.

Structural and environmental progress
The Kopter Group in Switzerland was founded in 2007 with the aim of building a new generation of turbine helicopters. Its Executive Vice-President (Technology) Michele Riccobono took AirMed&Rescue through the development of airframe design and manufacture since Sikorsky got his VS-300 up in the air – progress that has resulted in the shape and performance of the medevac helicopters we see today.
“The past 30 years have seen an evolution mainly in the areas of materials which, in turn, drove design and manufacture. All helicopter airframes produced and certified in the 1970s and 1980s were manufactured using aluminum structural elements riveted together. With the availability of composite materials in more recent years, a series of structural elements started to be produced using these new materials, initially with glass fibres then honeycomb, and finally full carbon fibres.”
As is often the case with advancements in the aviation industry, what slows down the introduction of new equipment is the lengthy certification process, explained Riccobono: “The introduction of these materials has been progressive due to the certification burden; the need to establish new certification requirements and guidelines for material qualification. Initially, secondary structures, such as doors and cowlings, started to be produced with composite materials, taking advantage of the easier modelling and reduced complexity in serial manufacturing once the proper tooling had been developed.”
Step by step, though, the development of the material continued: “A series of hybrid structures mixing composite and metal started to appear, to switch later to a full composite structure in which different elements are either bonded or riveted together … basically using the same assembly concept of metallic structures, but producing the individual elements out of composite. This is now being pushed further forward to develop a full composite airframe in a monococque configuration: the entire fuselage is made of a single part. But this has so far been done only with small helicopters – two seaters – due to the complexity in certification and production.”

The use of carbon fibre, added Riccobono, is also beneficial for safety. “It allows us to create a structure that has a level of crashworthiness equivalent to that of a conventional metallic structure but with a much lighter weight. Carbon fibres also make it easier to model complex aerodynamic surfaces that enhance the helicopter’s performance, and we have adaptive manufacturing using 3D printers for producing even complex moulds. Carbon fibre or composite structures also offer better damage tolerances and a very long service life, especially for primary structural elements such as helicopter rotor blades.”
Talking of progress, Honeywell in the US points to the ‘continuous improvement’ in helicopter engines over the years. “Since Honeywell entered the aircraft propulsion market in 1953,” said Karina Larsen, Vice-President (Partnerships & Business Development), at Honeywell Aerospace, “we have overseen improvement programmes that have resulted in engines that provide more power, increased mission range, enhanced payload capabilities and a wider operating spectrum. There is,” she added, “an ever-growing need for engines that require less maintenance, have more intuitive design, and benefit from lower fuel consumption. Modern engines are certainly expected to be more fuel efficient.”
Riccobono at the Kopter Group reports that turboshaft engines are now being developed with requirements that were not, until now, rated as being of primary importance in a world that was largely unworried by climate change and aircraft noise. Times, though, are changing: “Low specific fuel consumption, reduced CO2 emissions and lower noise levels are requirements of the airplane engines that are now being imported into the helicopter market. Additionally, the reliability of engines is being increased significantly not only by their design but also by the availability of control systems
the reliability of engines is being increased significantly not only by their design but also by the availability of control systems
– such as Full Authority Digital Engine Control – that constantly monitor the engine’s health. This enables the early detection of degradation that, if not discovered, could lead to engine failure in flight.” This enhanced reliability is bringing more choice to the industry, he added: “The use of single-engine rotorcraft is now being considered more and more for missions such as helicopter emergency medical services for which in the past only twin-engine helicopters were used. This is particularly beneficial because it reduces operating costs and, because it’s more affordable, it ultimately increases service availability.” Kopter’s own helicopter, the SH09, is being developed as a game changer, since it ‘offers the cabin space, performance and safety standards of a twin-engine helicopter for the price of a single’.
Operator POV
One of the best ways to determine the optimal features of a 21st Century air ambulance helicopter is to talk not only to the manufacturers, but also to the people who actually operate and fly them across all terrains and in all weathers. The Dorset & Somerset Air Ambulance Service in southern England ran 1,197 missions – that’s 23 each week – in the year ended March 2018 in a twin-county coastal region popular with hill walkers, sailors, swimmers, anglers and surfers, and bordered by busy shipping lanes. Last year, it decommissioned its Airbus Eurocopter EC135, which carried two crew and two patients, and replaced it with an £8-million AW169, a twin-engine, 10-seat helicopter developed and manufactured by Italy’s Leonardo Helicopters, AW’s re-branded identity.
The new machine was necessary, says the service’s CEO Bill Sivewright, because changes in the region’s hospital network meant that patients with major trauma conditions would have to be flown to centres farther away than was previously the case. “Without a major trauma centre in Dorset or Somerset, we therefore needed the ability to be able to fully treat a patient en-route to hospital. Further examination of the requirement also revealed something quite simple: if the patient was at the centre of our thinking – and on-scene the patient is at the centre of the ‘treatment zone’ – should the patient not be at the centre of the cabin of the air ambulance? Once this logic was applied, the choice of a successor aircraft was quite straightforward. That is not to say that factors such as cost, safety, and potential for night operations were not considered, but only one platform offered us the cabin format to meet our fundamental requirement.”

The unit’s chief pilot Mario Carretta highlights the improved medical and flight capabilities of the AW169 compared with the machine it replaced.
“The main flight improvements are the increased load capacity, so we can carry extra fuel, equipment and people. The main difference clinically is that our team has complete access to the patient, head-to-toe. That means that they are in a much better position to help a patient if there is a problem en-route to hospital.
He continued: “Having the greater endurance allows the helicopter to cover a much wider area than before and means the aircraft can complete more tasks without the need for a re-fuel. Having fully integrated traffic collision avoidance, helicopter terrain awareness and synthetic vision systems increases the pilot’s situational awareness and helps to reduce the workload, particularly at night and in poor weather. The aircraft’s single-engine performance is also impressive.”
The service, which takes patients to 14 hospitals across the south-west of England, says that the AW169’s night flying capabilities mean that it can undertake full night medical missions. Pilots can fly directly to the patient without the need for any fixed or pre-established lighting, described as a ‘significant’ advantage.
The AW169 was not in fact bought by the service which, like many air ambulance units in Britain, is funded largely by charitable donations instead of the state. “It is leased,” Sivewright told AirMed&Rescue. “This was the most cost-effective way to procure such an expensive asset. If we owned the aircraft and for whatever reason it needed a major component replaced, the charity would have to meet the full cost of repair. That is a risk that we felt was not justified.”
Three other air ambulances services in England are using the AW169, and it’s been ordered by medical and rescue operators in Sweden, Switzerland and New Zealand.

What’s on the inside
As ambulance helicopter airframes evolve into what are almost flying treatment rooms, attention is turning to making the most of the increased space available with interior fittings that are light, functional and easily adaptable. In Austria, Helikopter Air Transport (HAT) has designed Kokon, a carbon fibre modular medical interior lining that has been installed in the twin-engine Airbus H135 helicopters used by the company’s air ambulances. Kokon, says HAT, is a ‘superior, stylish and minimalist alternative to standard interior panels’. Manufactured in Innsbruck, its features include:
- A total payload capacity of 76.5kgs/166.4lbs directly on the interior lining
- Flexible and fixed mounting positions for varying loads and dedicated containers for medical equipment, which increases cabin space
- Easy and fast change of equipment configuration
- Smooth cladding that makes helicopter interiors seem larger than they actually are
- Availability in different colour schemes
- Quickly removable to enable access to airframes
- Customisable, with or without sound proofing
- Cleanable with standard disinfectants and detergents.
Wolfgang Burger, the company’s Technical Director, told AirMed&Rescue: “It’s a multi-purpose, carbon fibre interior liner is designed to get more medical and other equipment into smaller spaces – to maximise available space – so that the cabin area for crews is wider, and the smooth cladding makes the interior space look even larger. The design can be adapted for use in different helicopter airframes.”

At Cobham’s Aerospace Communications division in South Africa, Regional Sales Director Andrew Legg flags up an avionics problem – or challenge – for helicopters. “Cobham has always prided itself on reducing the weight and cost of satcom products. While our equipment is one of only a few accepted standards in the industry for fixed-wing airframes, rotary wing platforms remain a challenge for satellite communications. This is due to interference caused by the chopping of the signal by the helicopters blades, which rotate between the antenna and satellite.” The effect of this ranges greatly based on the nature of the blade composition, blade dimensions, the satcom system’s antenna location and area of operation of the rotary wing platform, explained Legg. This means that helicopter applications can work either very well, moderately or with difficulty.
Integration and proof-of-concept operation testing, he said, ‘are therefore mandatory in any installation planning prior to fleet roll-out of a satcom solution. There are solutions to this problem and we continue to explore these with our partners in the industry’. “One such solution is the HDR Bearer offered by Inmarsat on its SwiftBroadband Service. While this solution works well in principle, it has a niche market in that it really serves only high throughput customers moving video off the platform. It’s not cost effective for general connectivity. We do have product working successfully on a range of platforms from the Bell 407 to the AW101.”

Honeywell’s Karina Larsen agrees that helicopters present communications and connectivity problems, but says they can be overcome. “They are a challenge because rotor blades can interrupt satellite signals to and from rotorcraft. But with a digitised solution, such as our Aspire 200 Satellite Communications system, we see significantly enhanced capabilities for reliable, connected communications for helicopters.
“Connectivity is becoming a necessity onboard; safety, maintenance, and real-time data can all be enhanced with connected services, and it can also help with fuel economy. Consistent connectivity is very important for helicopter operators. It enables critical communication between the aircraft and the ground and allows passengers to stay connected while they are in the air. Connectivity effectively turns an aircraft into an information hub, providing a stream of data to and from the aircraft. Whatever its mission profile – air ambulance, government use, oil and gas transportation, VIP/executive transport and others – connectivity greatly enhances the modern rotorcraft.”
Honeywell also flags up developments in navigation systems. “They are specifically built,” Larsen told AirMed&Rescue, “to withstand the often hot and dusty conditions that rotorcraft operate within. With our ring laser gyro technology, we provide pilots with incredibly accurate positioning data and maximised safety even during extended periods of operation.”
The latest avionics suites available come with scalable architectures that can be tailored to a variety of helicopter designs, said Kopter Group’s Riccobono. “They collect and analyse a large volume of data in an intuitive environment, significantly reducing pilot workload. The increase in pilot situational awareness is the result of cockpit designs that prevent human-factor related errors that are still the major cause of aviation accidents.

“Kopter is the first original equipment manufacturer to partner with Garmin for their new G3000H avionics suite, the best-in-class situational awareness system enabling a higher level of safety for every mission. The large dual landscape-oriented displays and single touchscreen controller can be configured according to customer requirements. Helicopter pilots can make the most informed decisions while operating in high workload conditions.”
Looking to the future, Kopter sees helicopter airframes getting even bigger, believes Riccobono. “They are likely to be larger, with a reduced number of parts, although switching to a full monocoque architecture is made difficult by the certification burden, especially for the reparability of impact damage. A reduced number of parts cuts assembly costs, but as increased investment for tooling is necessary, a careful balance has to be made in the design to develop a sustainable economic model. Some recent helicopter models have airframe sections such as the canopy produced as a single part, thus reducing manufacturing and assembly costs.”
Coming soon?
In Italy, Leonardo and the Politecnico di Milano (PoliMi) are developing new technologies for helicopters as part of their expanding collaboration, launched in 2016 with the signing of Innovation Hub, a multi-year framework agreement. “In Leonardo, we invest in continuous and increasingly collaborative innovation,” noted Alessandro Profumo, Leonardo’s CEO.“[We aim] to develop increasingly effective and sustainable solutions for our customers and for Italy.” The multi-year collaboration with the Politecnico of Milan is a concrete example of this. “By putting our wealth of skills in line with those of the academic world,” added Profumo, “we can accelerate the processes of innovation and technological development, create synergy and mutual benefit to support the competitiveness of Italy.”
Through project Comfort, Leonardo and the PoliMi are developing technologies to reduce the vibration and noise of helicopters, and the reference platform for the study is the AW139 helicopter
Through project Comfort, Leonardo and the PoliMi are developing technologies to reduce the vibration and noise of helicopters, and the reference platform for the study is the AW139 helicopter. The research activities are concentrated on three main areas: the rotor, from which the vibrations originate; the main gear box attachments, through which rotor vibrations are transmitted into the helicopter structure, thereby reducing the level of comfort, and finally on the airframe itself. The ultimate goal of the programme is to demonstrate a significant vibration and internal noise reduction, through the co-ordinated use of passive and active systems.
Elsewhere, the shape of air ambulances to come could be the pilotless Cormorant, built by Israel-based Tactical Robotics. It could be used, if and when it’s operational, for battle area medical evacuations. At a demonstration in northern Israel in 2015, the one-ton Cormorant – with a mission range of approximately 30 miles – carried 1,000 lbs. of cargo and a medical training mannequin at speeds exceeding 100 mph.
Powered by a single turboshaft engine of the type used in conventional helicopters – but with two smaller, contained rotors instead of one large one on top – its physical footprint is reduced, a big advantage in urban, wooded and mountainous environments. The company – which hopes the bug-shaped Cormorant will be bought by Israel’s defence force and the US military – says that it can operate in winds higher than those with which a human helicopter pilot would be comfortable. Patients – it can carry two if there’s no cargo load – would be connected via a remote monitoring system to ground staff able to check their vitals and talk with them on a two-way video link. Tactical Robotics says the carbon-fibre airframe should help it to dodge radar detection, while its exhaust system can be air-cooled to reduce its infrared signature.
Science fiction, or a reality coming to a helicopter ambulance station near you?
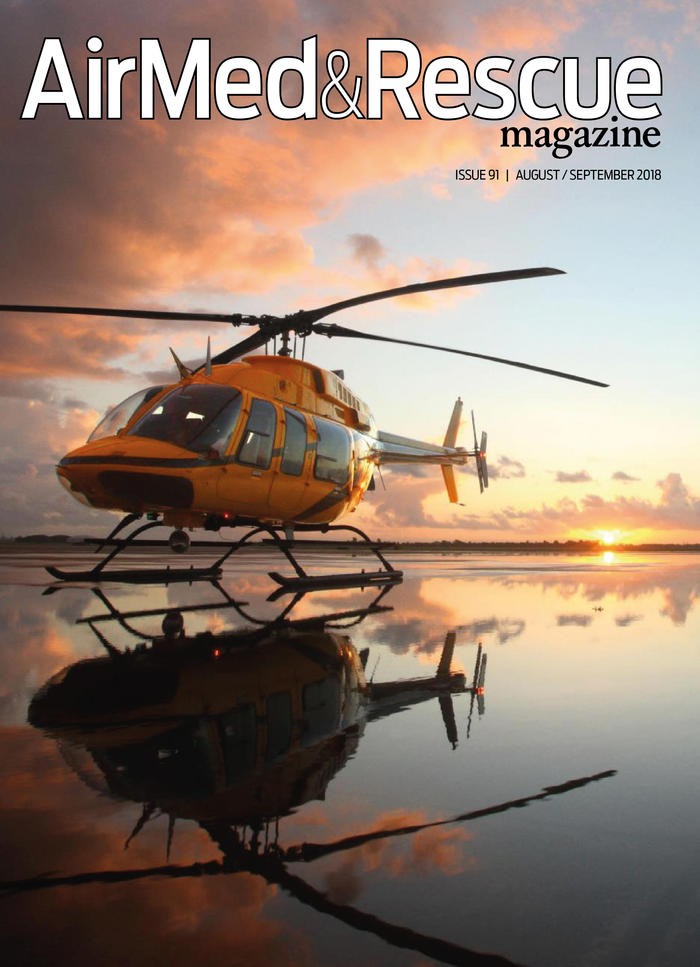
August 2018
Issue
In this issue:
Night riders - The ever-increasing availability of night vision imaging systems onboard helicopters and the regulations surrounding them
Electric avenue - Electronic flight bags are changing how pilots work
I, robot helicopter - The latest generation of helicopters are lighter, faster and better equipped
Costs of medical transport in Florida come under scrutiny
Aeromedical transport training in Bangkok
AirMed&Rescue Magazine attended the 2018 annual Air Centric Personnel Recovery Course (APROC) at Gilze-Rijen air base, The Netherlands
Focus on helicopter evacuations in Nepal
Working to the limit -Fatigue management in the world of international medical repatriations
Creating the right culture -Bruce Webb, Airbus pilot, offers his thoughts on leadership and the culture of safety for crewmembers
Profiles
Capital Air Ambulance
AIUT Alpin Dolomites
Airbus Helicopters
James Paul Wallis
Previously editor of AirMed & Rescue Magazine from launch up till issue 87, James Paul Wallis continues to write on air medical matters. He also contributes to AMR sister publication the International Travel & Health Insurance Journal.